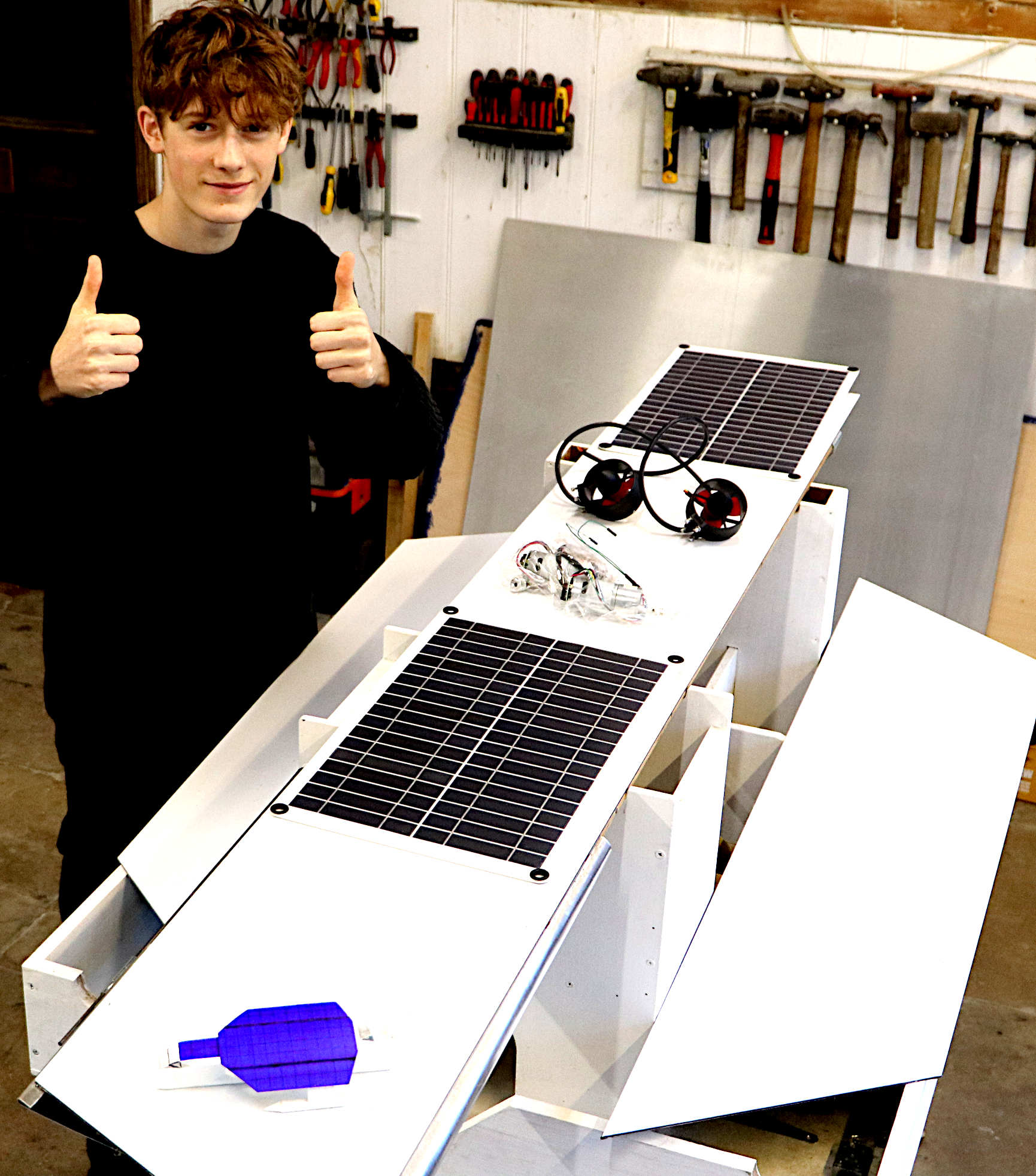
Here
we are in February 2024, facing fresh challenges. This time
upgrading an existing motorised display for conferences and
exhibitions. The stand was last displayed some time ago at
Hastings Museum, Ocean
Symposium 2021. Our last outing was with the SeaVax
model, to a local United Nations
Association Climate and Oceans (UNC&O) event in Bexhill-On-Sea, not far from
Hastings and the famous battle
in Sussex in 1066, in November
2023.
Our
challenge for 2024, is to modify the mountings, to take the
"Queen
of the Nile." A 1:20 scale model some 3 meters in
length. So, roughly 900 millimeters longer than the SeaVax.
With a proportionate weight increase and diameter needed for
any exhibition stand.
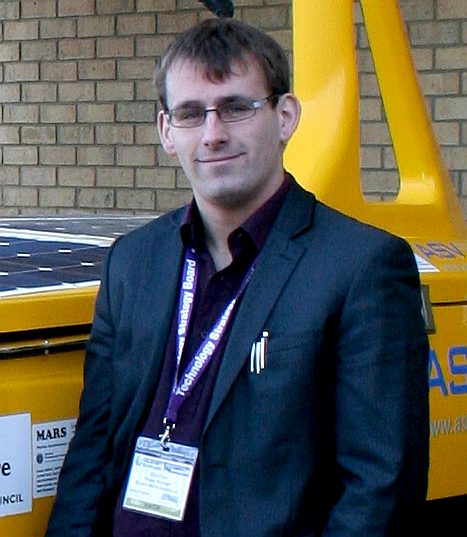
|
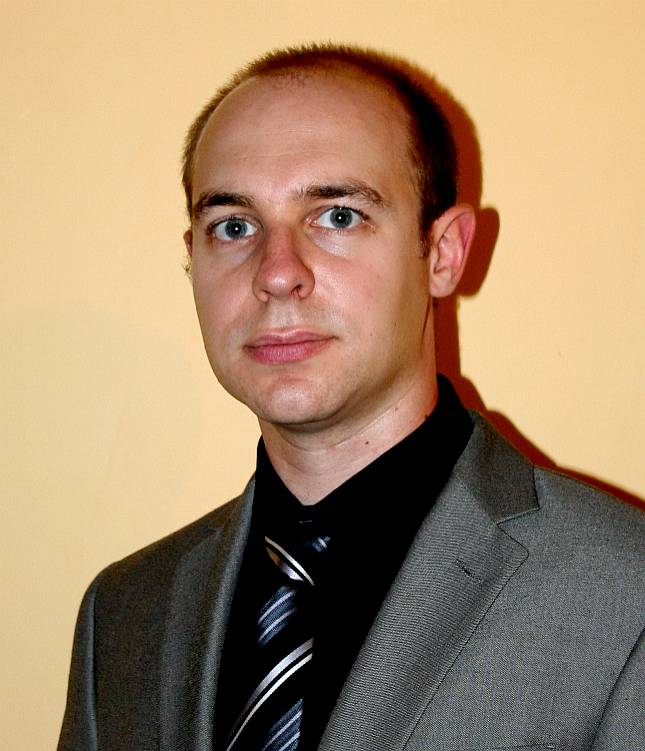
|
Chris |
Richard |
SEAVAX
PROJECT
MANAGER & PURCHASING SPECIALIST -
Chris and Richard rolled up
their sleeves over the August Bank Holiday to help design a stand for the
Innovate2015 show. The challenge was to build a space saving display
that would be portable and capable of being adapted for other events in
2016. Little did they know that their efforts would be rewarded in 2024
as part of an EU Mission. This time promoting solar and
hydrogen powered marine transport.
The
revolving show stand we are modifying for the "Queen of
the Nile" 1:20 scale model of the proposed river
and coastal cruising yacht, was originally fabricated from
steel section odds and ends
in the workshops in Herstmonceux
Museum, Sussex,
England. This started in
2015, as part of the SeaVax
project, some nine years ago. Part of the quest to prove that
it is possible to filter macro and micro plastics from
seawater. The experiments including constructing a water
test tank, and finally, attending events to show the
world that the concept worked, starting with one
in London at Innovate UK. Many more events followed, after
which the stand was consigned to long-term storage, rather
than being scrapped. Most fortunate, because it is now part
of a plastic display, including the 1:20 Amphimax support
vehicle.
BACK
TO THE DRAWING BOARD -
We have a dry marker board in our workshop
for brainstorming design sessions. In this case the team wanted to
fabricate a small stand that would be capable of tilting the 2 metre
model to 45 degrees - mainly to save on floor space. A secondary
objective was to produce a motorised option, for other events, where,
with suitable lighting the model could become an attractive feature.
These are the notes made by Chris while the team were working out what
was possible using items in the grounds. At this stage there is no
underlying theme, but one will soon develop.
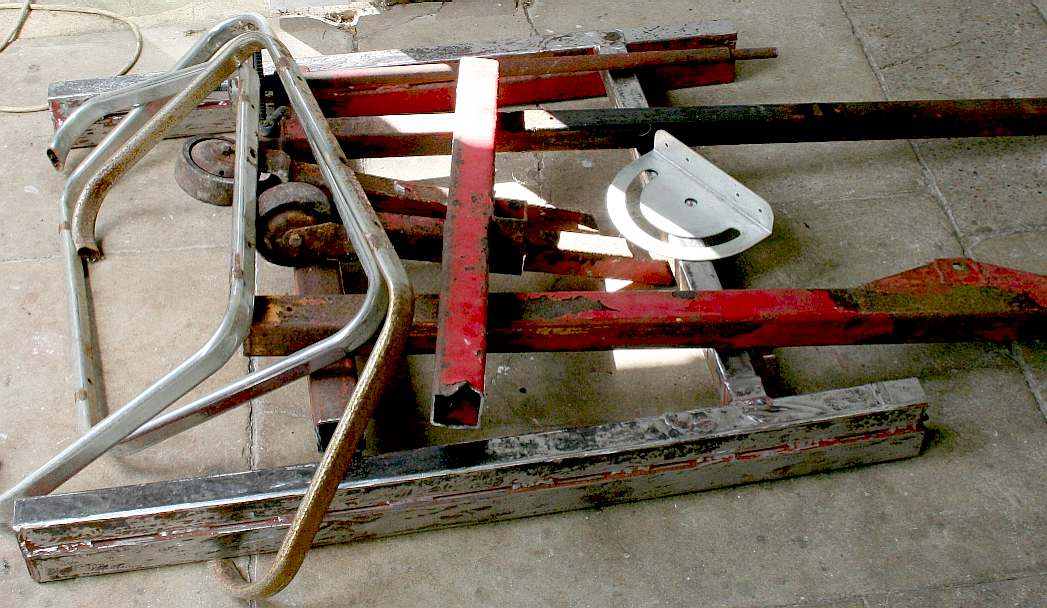
SCRAP
HEAP CHALLENGE
- Using only steel from items that were due to be sent to our local metal
waste handler (H.
Ripley & Co, Apex Way, Hailsham, East Sussex, BN27 3WA - T: +44 (0)1323 440672
E: info@hripley.co.uk)
the team accumulated a pile of donor parts - mostly from an old engine
hoist, that in the world of electric vehicles, was surplus to
requirements. From our experience we can say that H Ripley (known
locally as Ripley's) operates
their recycling yards to an exceptionally high standard. They also
support local innovation.
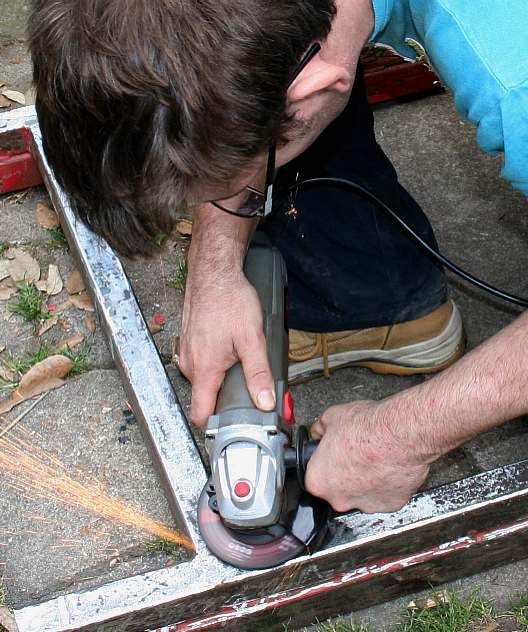
CLEANING
OFF THE RUST
- Chris grinding an earlier weld flat. The old engine hoist was 40x40 and
50x50 mm box (hollow) section steel tubing - the mainstay of hundreds of
industrial fabrications. All rust has to be removed to weld steel fresh.
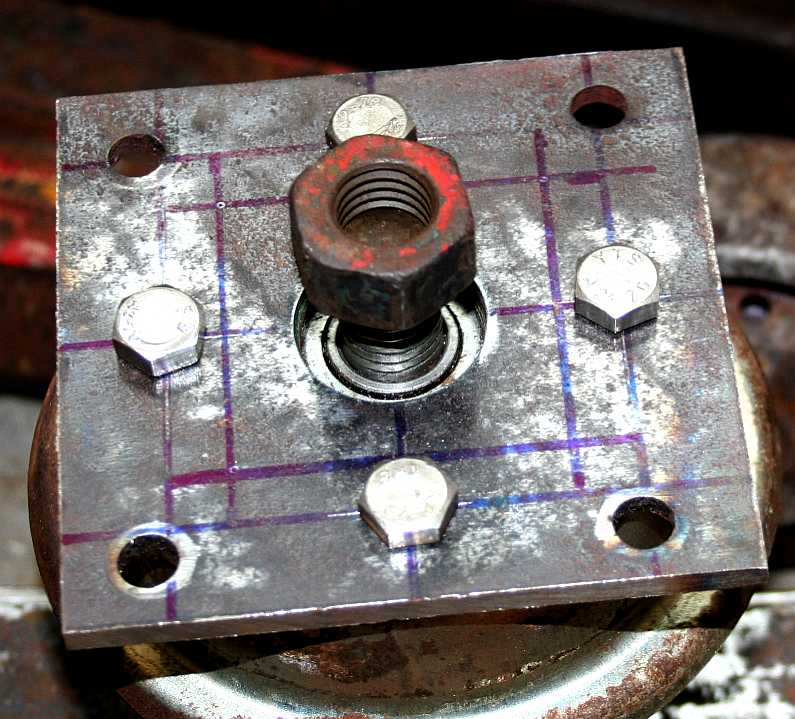
MK1
MOUNTINGS - Making the base mounting flange from 6mm steel plate. This has to be
accurate so that the mast remains rigidly upright, but still able to
rotate smoothly.
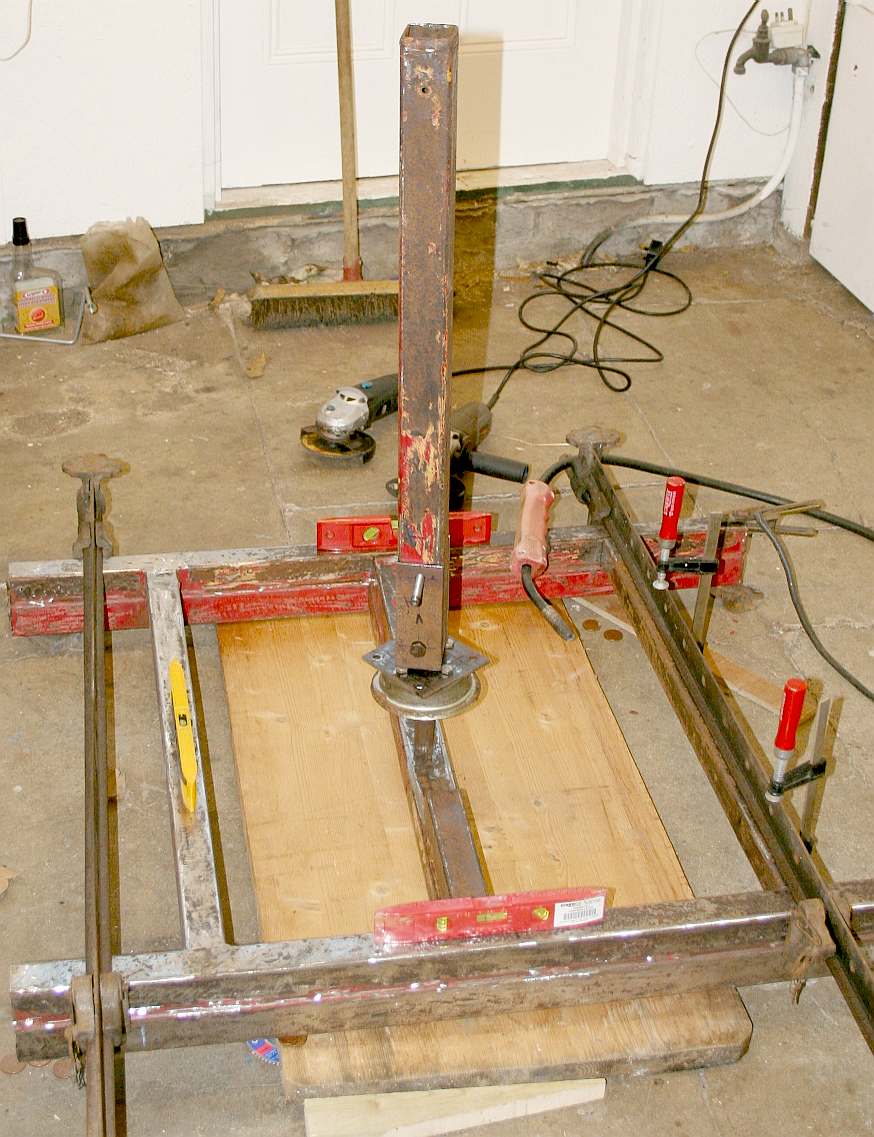
ON
THE LEVEL
- Very neat. The mast upright of the show stand bolts into two upright
plates (a fork) to clamp into position. The bearing assembly is very compact. No
motor drive is shown here. A 22mm solid steel rod (high tensile) comes up from a
50x50mm beam that is bolted into the stand base frame. Having tried this
hub bearing, we are not sure that it will do all we want in years to
come. It has too much play, either because the bearing tolerances are
not tight enough, or because the bearing spacing is not far enough apart
- or a combination of the two.
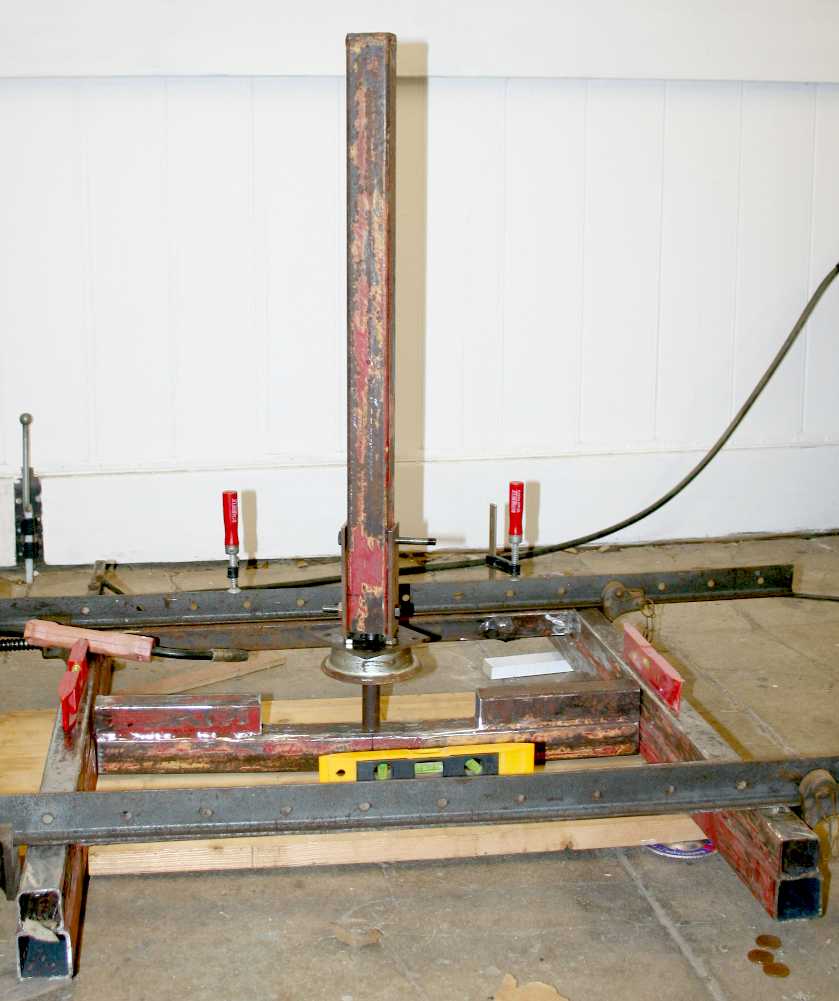
UPRIGHT
- Another view of the mast bearing mount. Note that the steel beam is
slightly curved. The steel spindle slots down a little further than
shown here, so that the motor drive unit mounts conveniently in place.
It does work, but we're looking for something smoother.
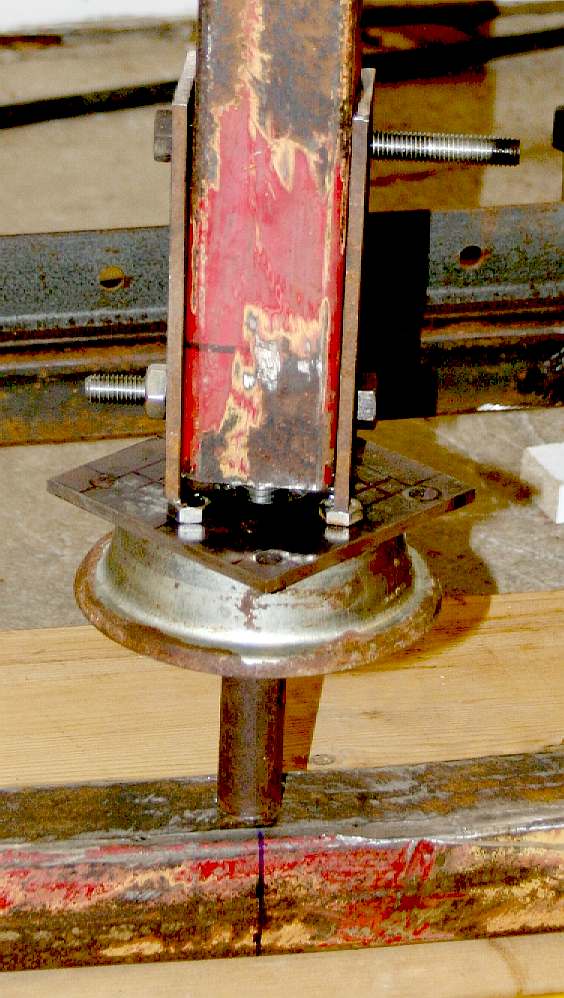
MOUNTINGS
- The uprights are also made from 6mm steel plate. They will be welded to
the mounting base flange. The high tensile 22mm solid steel rod shown
above is sturdy enough, but we are thinking about beefing up the
bearings from 36mm to 45 mm, with grease seals to allow prolonged storage
between events - without needing attention. See the alloy spider mount
below.
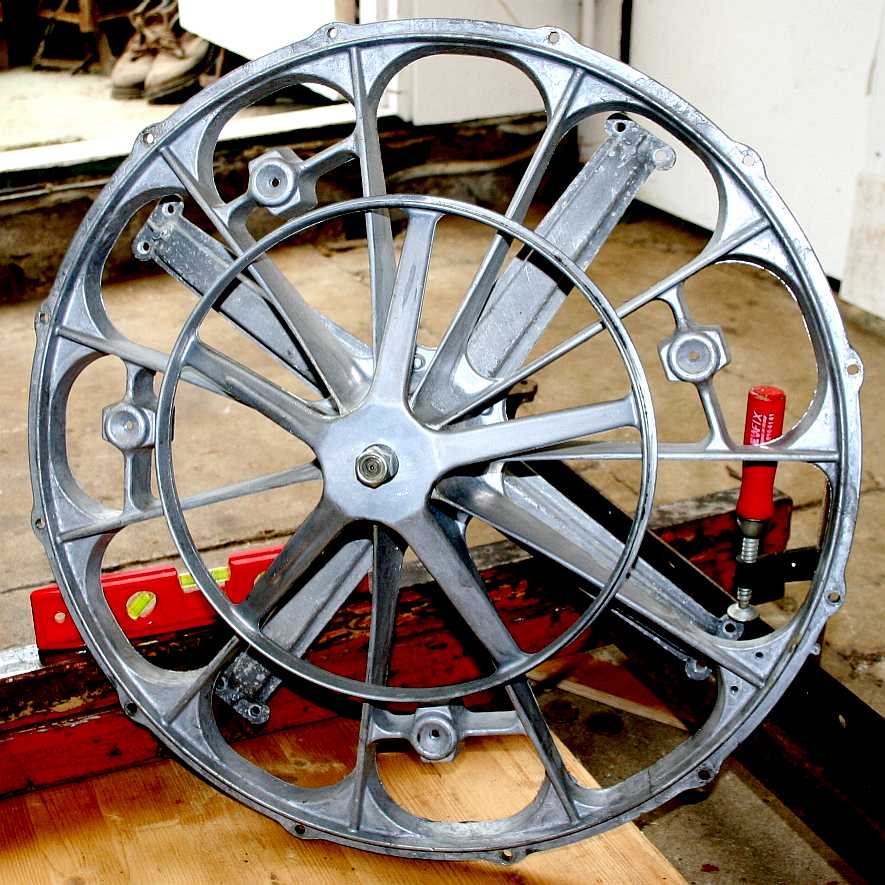
MERRY
GO ROUND
- The hub of this alloy (spider) casting contains two widely spaced 45mm
bearings with shaft seals to hold the lubricating grease free from
contaminants. A pulley wheel is attached to the end shaft on the
underside, being ideal to mate with our electric motor and reduction
box, via a belt that will allow clutching slippage. The clutching action
is to prevent people being harmed should they walk into the display. The
display will stop turning at the slightest touch - by design. A tension
wheel will allow adjustment of the rotation torque.
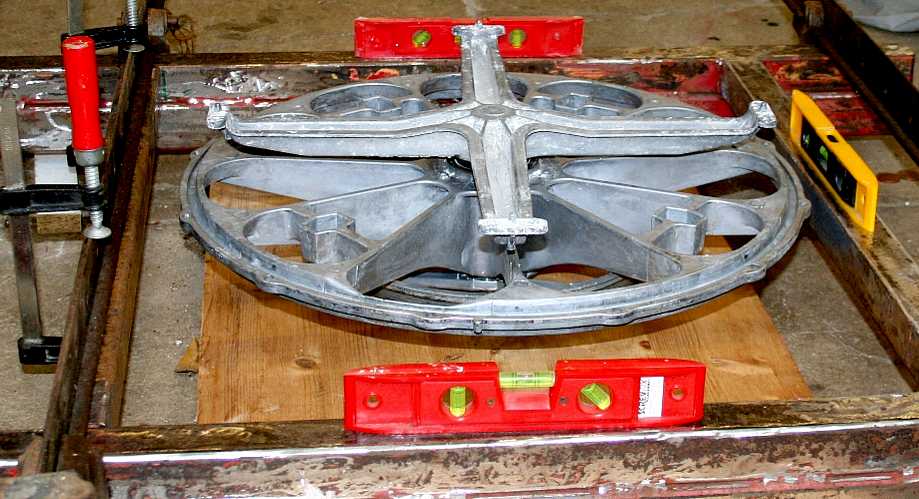
LINING
UP
- The mast mounting flange will bolt to the four pronged pedestal driver shaft seen
above. The base spider casting will bolt to steel brackets (not seen
here) on the stand base. The team will test out both designs before
deciding on which to use for this exhibition stand. The reason for
experimenting like this is because we are using this project to teach
our newer team members (those who are not our engineers) fabrication and
decision making on the hoof. There is nothing like a little practical
hands-on work
experience.
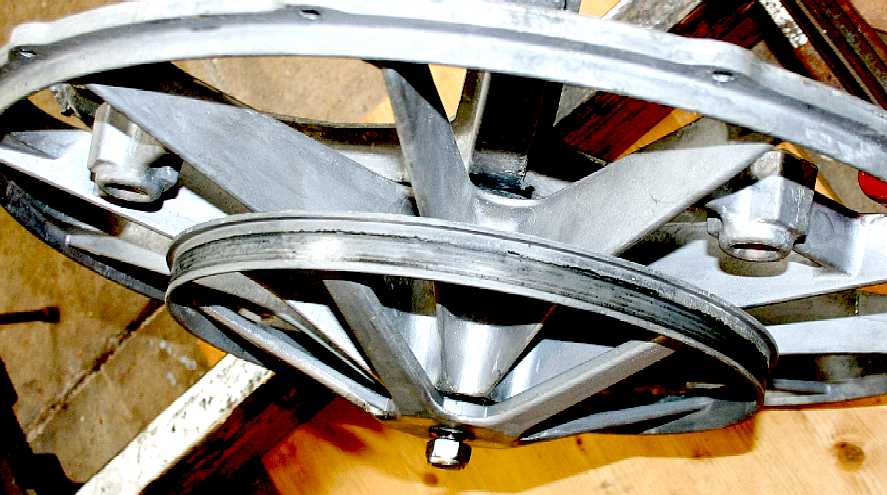
GROOVED
PULLEY
- The cast alloy pulley is precision machined to allow rotation speeds of
up to 1500 revolutions per minute. We only need one or two rpm, meaning
that the assembly is well and truly over engineered. It was this
principle that underscored the success of Charles Rolls and Henry Royce
when building their
Rolls
Royce motor cars, and that led to the
Merlin
engine, gas turbine engines for the 747 Jumbo
Jet and shipbuilding.
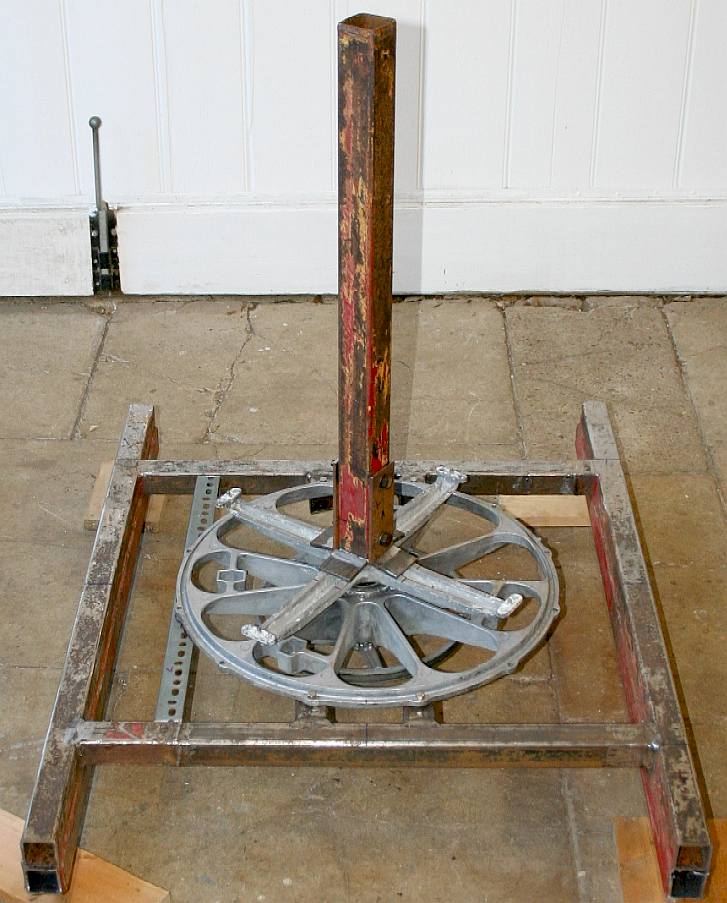
TEST
MOUNT
- Four steel lugs are to be welded in position and threaded to take 6mm bolts.
They are positioned above to check tolerances. On the underside of the main floor frame we welded in heavy duty 13mm
threads to take floor pads that are adjustable in height. This will
allow us to set up quickly on uneven ground in the full knowledge that
the SeaVax model is securely anchored to any showroom
floor (if you'll pardon the pun).
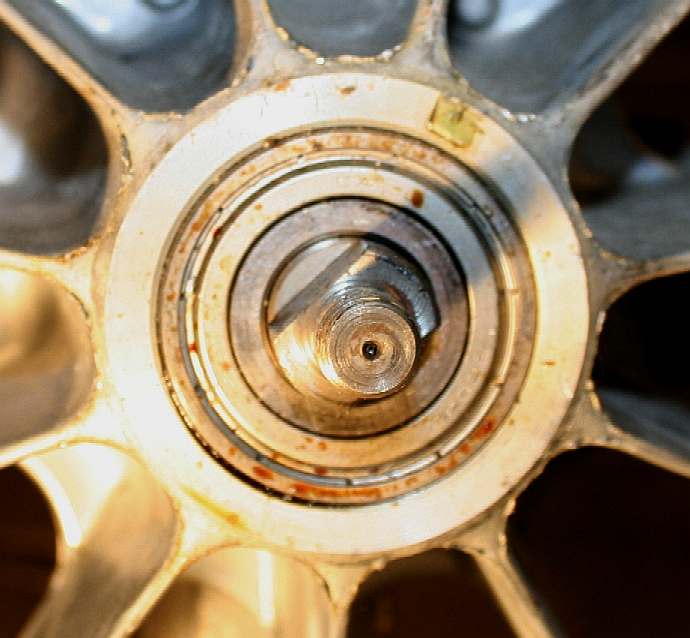
DETAILS
- LEFT: Lug detail showing that the top weld is ground flat to allow for
the deck cover
plate, or flooring, to lay flat on top of the frame. RIGHT: Bearings and drive shaft with the
pulley removed.
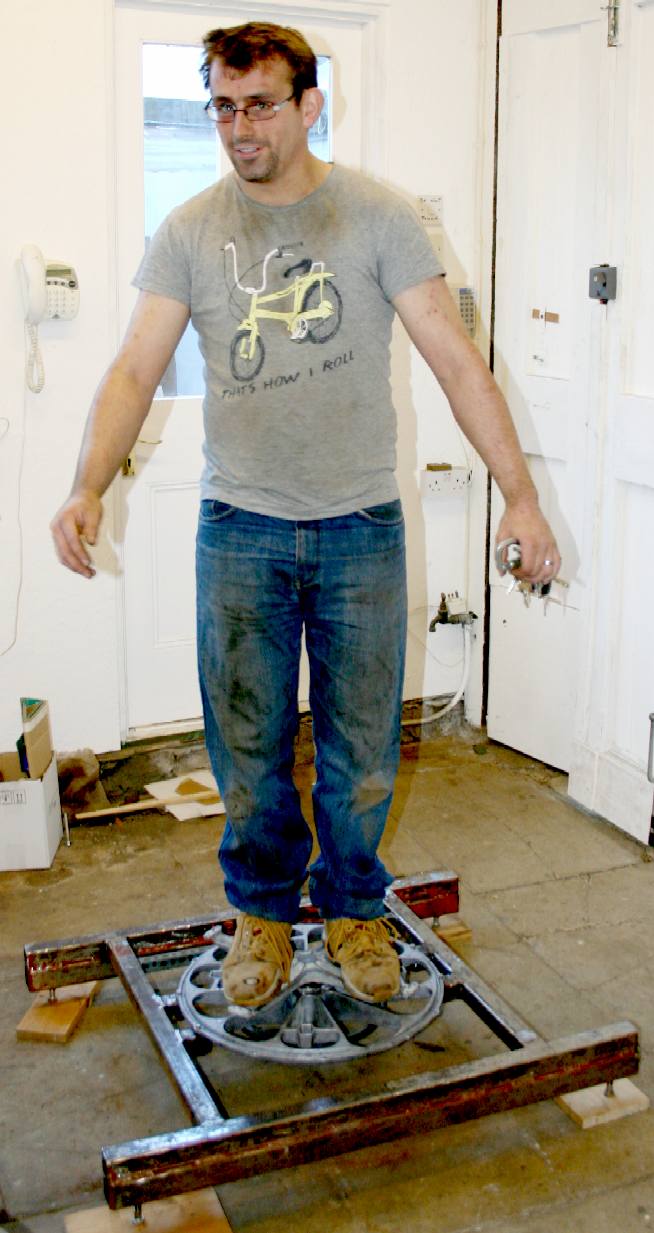
CRASH
TEST DUMMY
- Our project manager is not shy of getting his hands dirty. Having welded
in a lug or two, and bolted the assembly tight, he gave the bearing a
serious workout, by bouncing and swinging all his weight on the spider
swivel mount. This did not phase the stand at all - and this was with
only four mounts, when there will be another two at 180 degrees to the
first, giving six in total to spread the loads when operational.
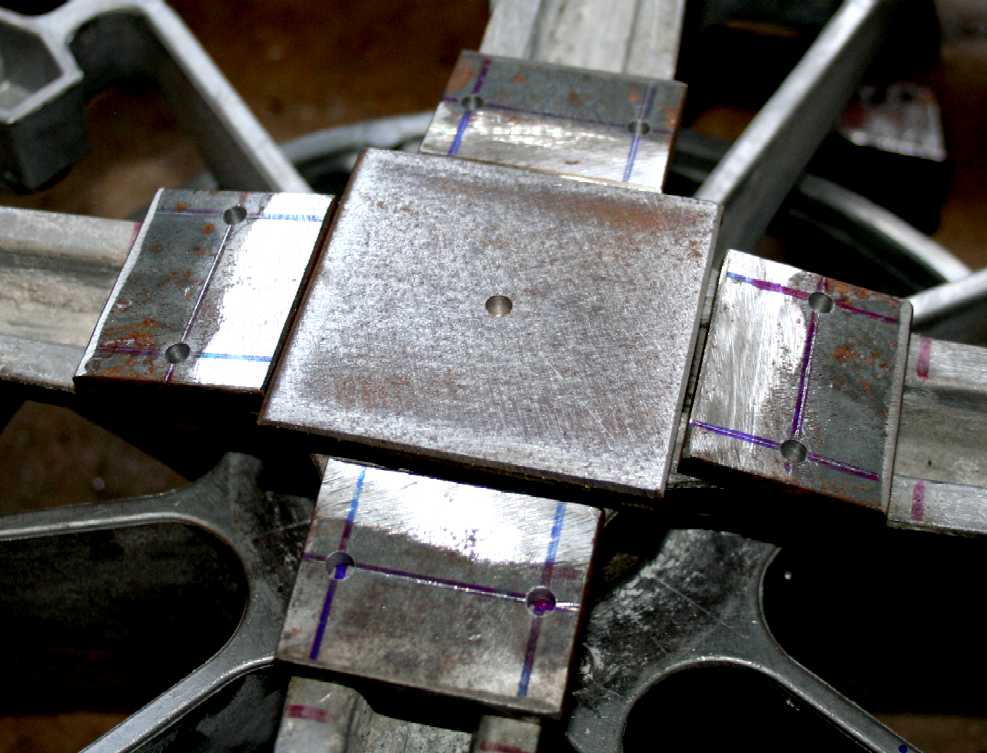
PEDESTAL
FABRICATION
- The four blank plates (cut by Richard, our logistics expert) are marked and drilled to form lugs that will be
bolted to the alloy spider. A centre bolt fixes the most important
(centre) plate in position. Being able to fabricate in steel or
aluminium is vital in any research and development workshop. Fabrication
involves high skill levels in marking out, cutting and welding. When welding thick section steel,
grind 'V' angles to ensure weld penetration. We don't just want a pretty
looking surface weld. 150 amps should do the job.
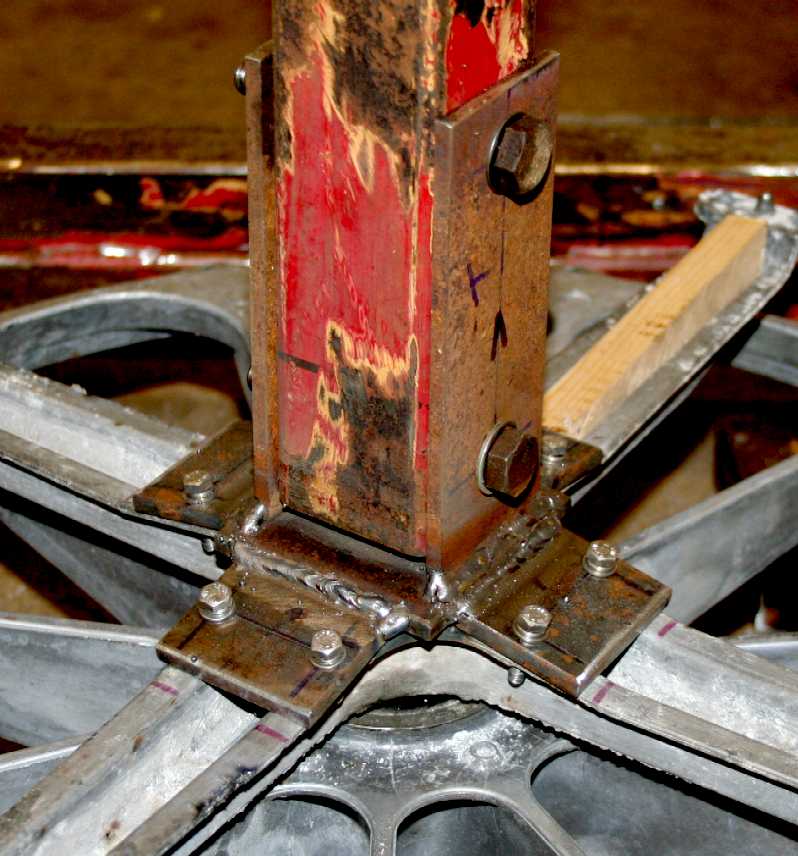
PEDESTAL
WELDING
- Is an art-form if you want to avoid distortion. You can see here that
the four steel lugs are bolted to the alloy spider. Tacking is the first
stage of the operation, turning quickly after each tack to complete the
opposite weld. Check alignment after each pair of welds. The mast
upright was fitted with magnetic spirit levels. The base was also fitted
with spirit levels. The mast was spun after each welding operation to be
sure it was upright. The steel and alloy needed to be cooled with
water
before the next welding operation. That is because we did not want to
melt the rubber seals or cook the grease lubricating the heavy duty
bearings.
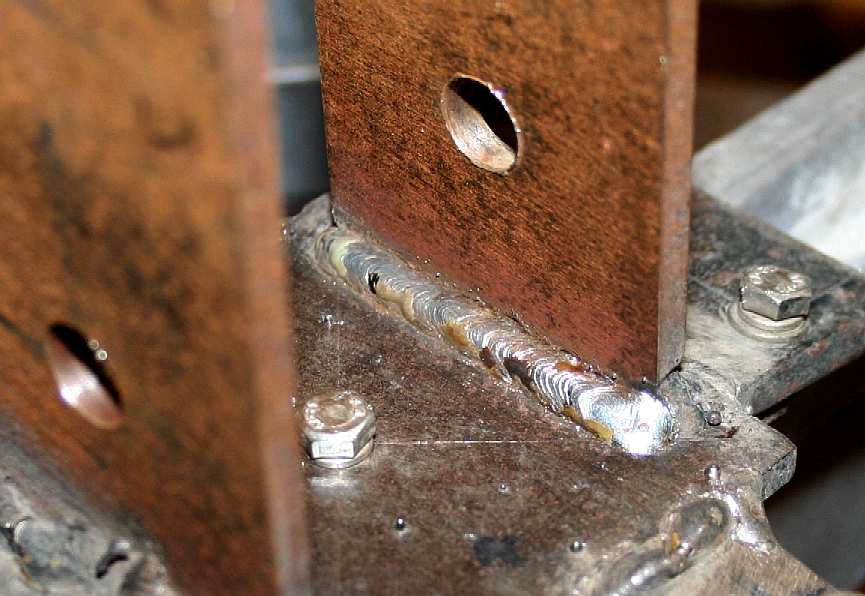
HAND
MADE - With the outside welds completed the mast was removed to
allow a bead of weld on the inner face of the upright clamps to the
centre base plate. If the assembly does not spin vertically, correctly,
after this stage - you are in trouble. You'll have to start again. If
the correct weld sequence is used, you will be okay. There is no
substitute for experience. Experiment on some scrap steel to perfect
your technique. MIG welding induces less distortion than TIG or gas
welding. Though TIG and gas welding give smoother welds.
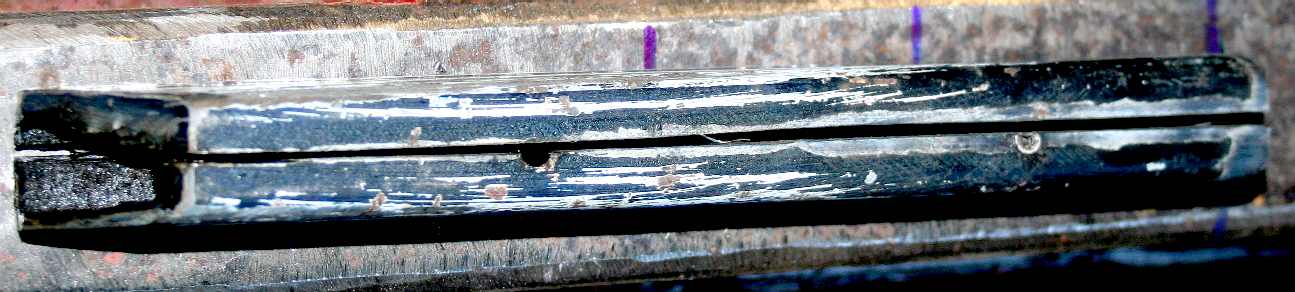
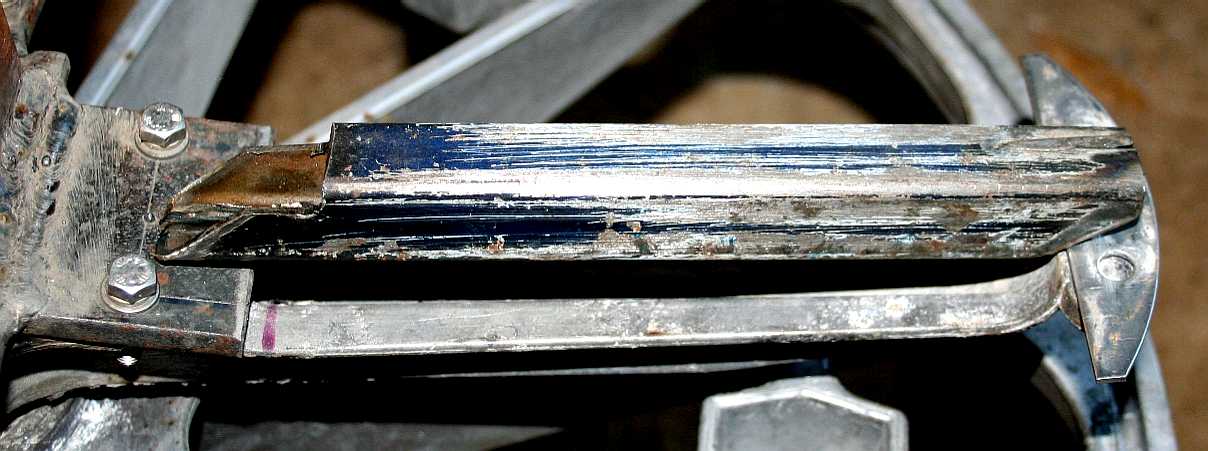
RADIANS
- We now want to take the strain out to the end of the cast aluminium
spider. These radians will also be the mounting for a rotating disc for
a light display. Box section steel 20 x 20mm was used for the radians.
They had to be cut to length and the ends cut to shape. A wooden
pattern was used to get the angles right. The tricky part was cutting a
3mm groove in the underside of each radian.
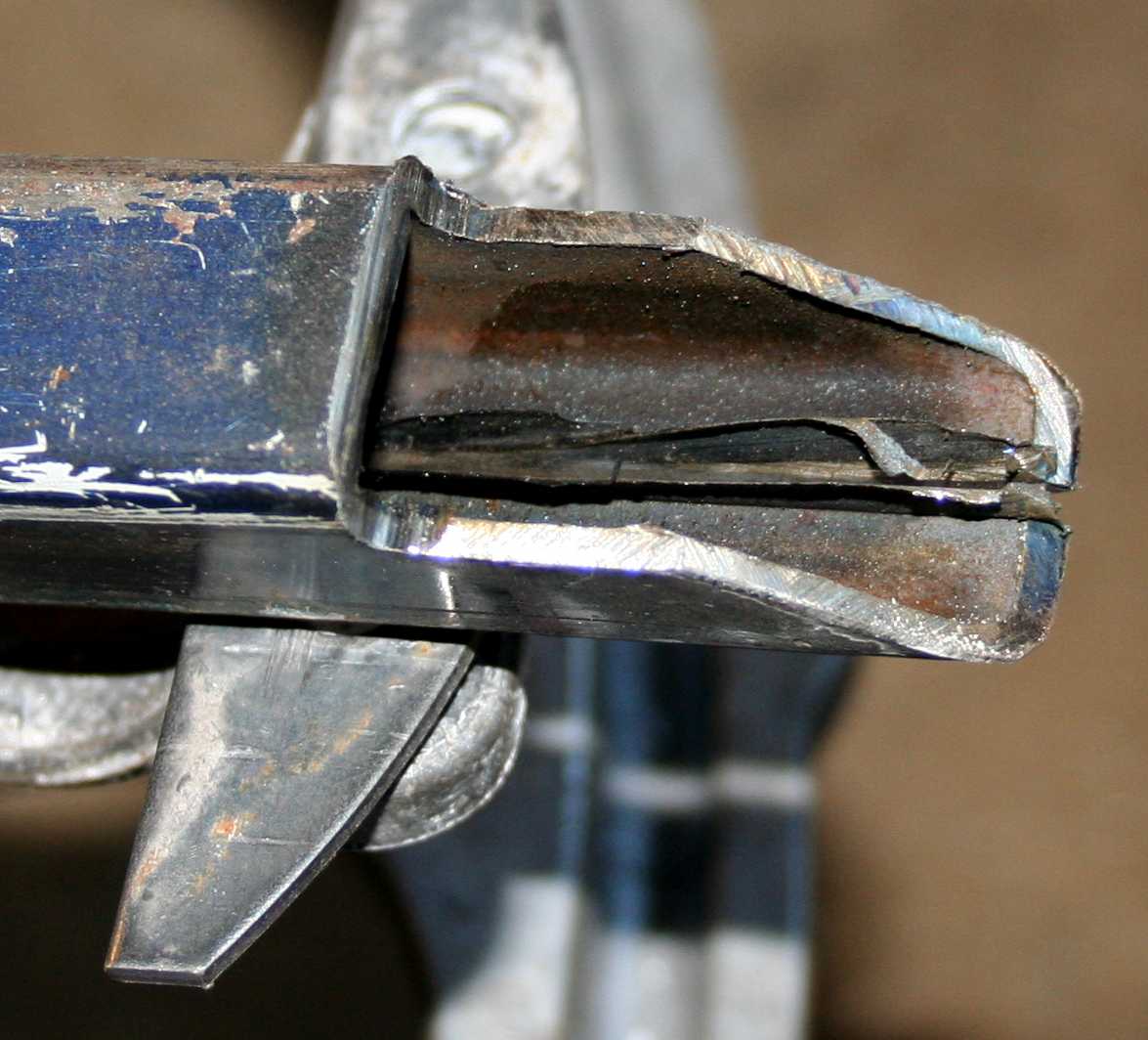
PEDESTAL
RADIANS - There are four radians, so the process had to be repeated
four times. See the end detail on the right. The cut down the middle was
to allow us to match the inner angle of the alloy spider. The radians
then fitted snugly within the arms.
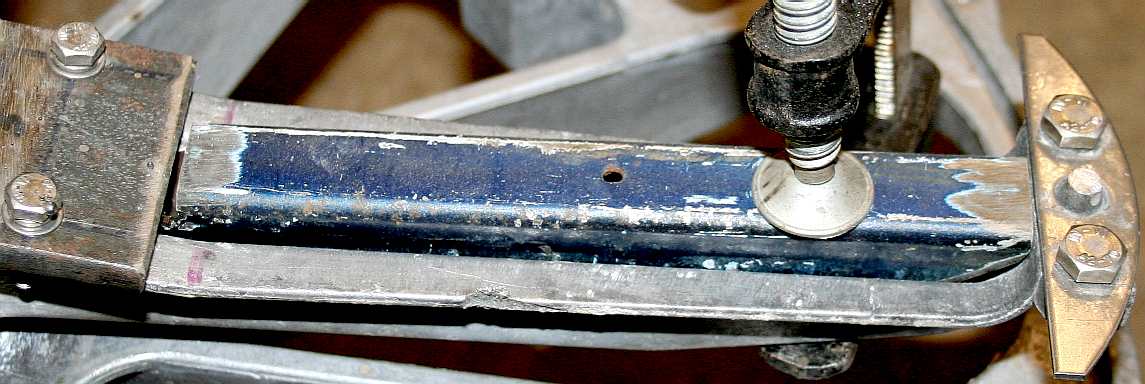
CLAMP
IT - Fabricating intricate components means getting the parts just
right, and then lining them up perfectly - and clamping them in place
for welding. Leave a suitable gap when welding thick sections if you
want to achieve full penetration. Note the bigger gap on the left for
6mm steel and a smaller gap on the right for 3mm steel.
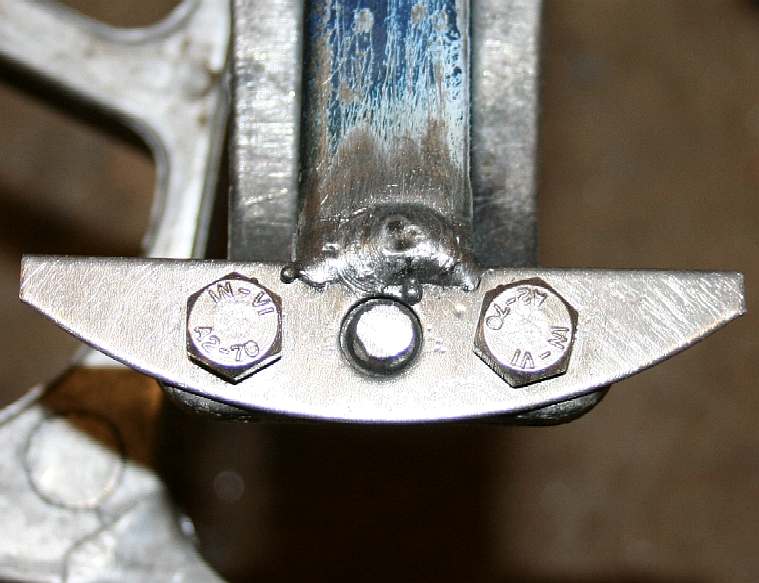
MORE
WELDING - Having made the parts fit so well, all that remains is to
weld them in place. We want full penetration without melting the aluminum
spider underneath. You can see from the pictures above that we managed
it. We did not change the welding settings, the operator just adjusted
his welding speed. Concentration is needed for each weld. Make sure you
are comfortable when welding, or your focus will wander.
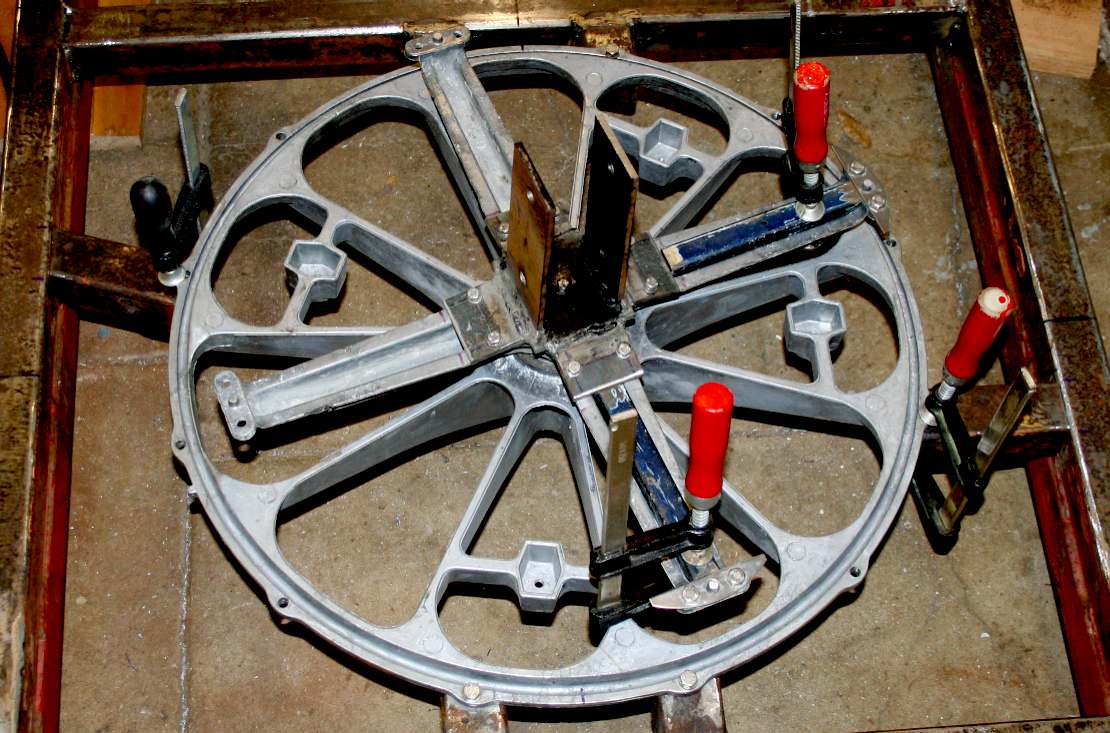
MERRY
GO ROUND - It looks for all the world like some kind of fun fair
attraction at this stage. You will not be able to see the alloy spider
once the stainless steel cover is fitted. The frame will also be covered
in, to prevent the inquisitive public from trapping their fingers.
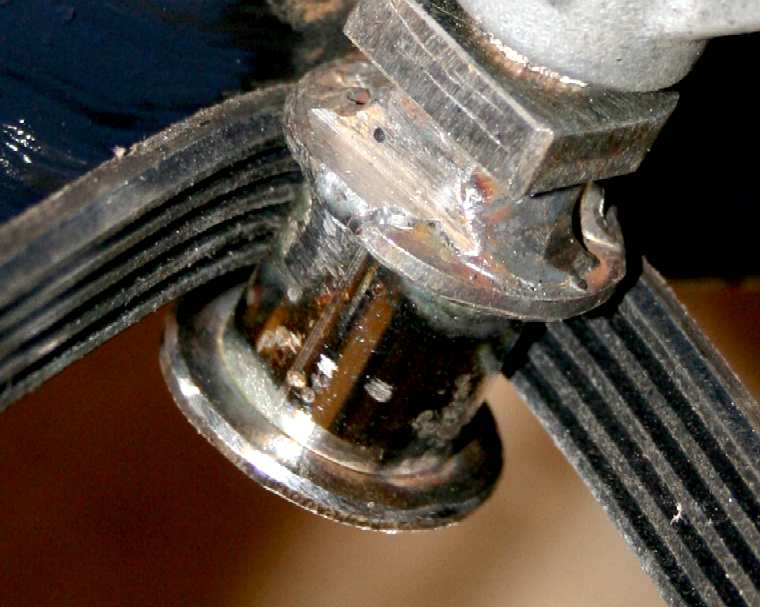
DETAILS
- LEFT: Adjustable feet - a chunky nut was welded to each corner with
the bolt head let into a load spreading foot (not shown). RIGHT: The
motor driven pulley (capstan). Normally a small drive pulley like this
would be grooved to mate with the rubber drive belt, so increasing
friction area. We want to keep drive traction to lower levels to provide
safety clutching, so have not machined in the V grooves, but have a rim
like on a cotton-reel, to keep the belt aligned when horizontal. These
belts normally operate vertically.
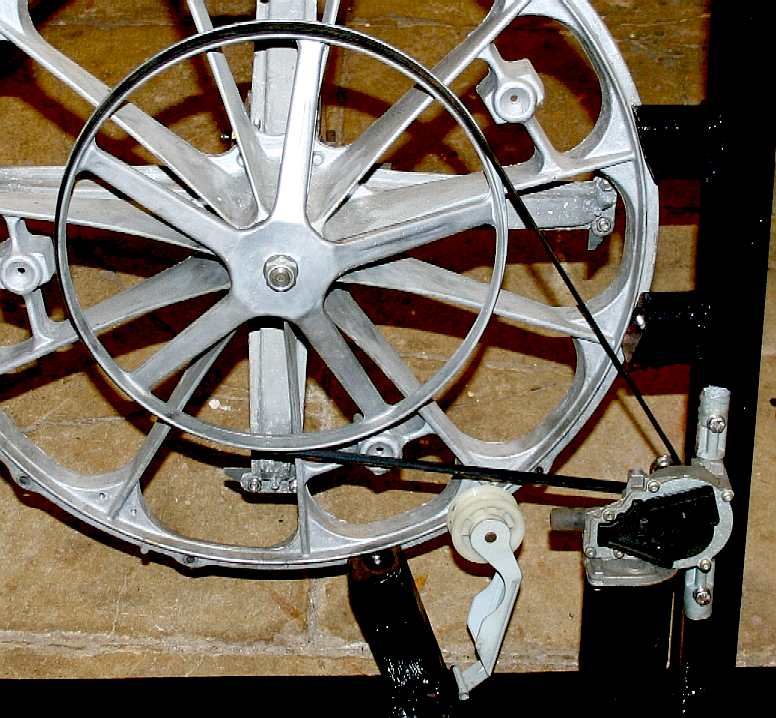
DRIVE
BELT - A small two-speed electric motor and reduction gearbox are
used, in this case a windscreen wiper motor that is being recycled. This
is the view from under the stand. Note the nylon tensioner/follower
pulley wheel, not yet fitted. There will be two of these on either side
of the drive pulley to give us precise control of belt tension. Springs
will be used to apply the required tensive force. Once you have the base
engineering sorted, you can add all kinds of gizmos. Compare the Ford
Model T with a modern Ford Focus. The basic design is the same: an IC
engine driving two road wheels. But the electronics onboard even this
everyday car, take the basic concept to a new level. We could have a
field day jazzing up this stand with sensors, voice or heat activated
messages, following passers by interactively. Even a powered tilt head.
You name it, electronics can do it. No time unfortunately - and the
robot boat is the attraction not the stand - a concept vessel brim full
of electronics and innovative design.
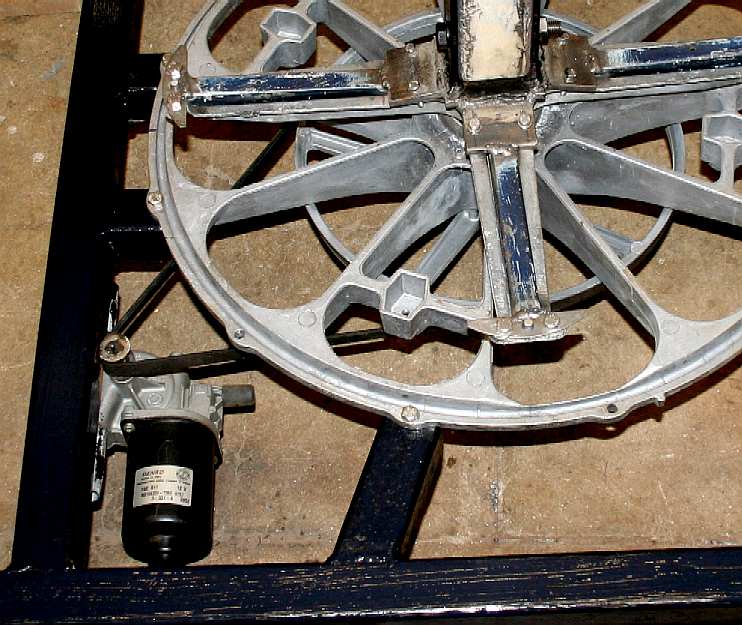
MOTOR
POSITION - Seen here from above, the motor drive is neatly tucked
into one corner. A decorative cover will protect the motor and belt
drive. It could not be more simple - our motto:
KISS.
We may use a heat-sink rather than a cooling fan for this stand, to keep
the noise levels down. The stand will be run for 48 hours while
monitoring the temperature - just to be sure nothing is strained. It is
more likely to be the power pack that causes heat build up. We have
tested a step down transformer unit that will fit nicely, but not yet
run it for any length of time. Correct alignment of the belt and pulleys
is essential.
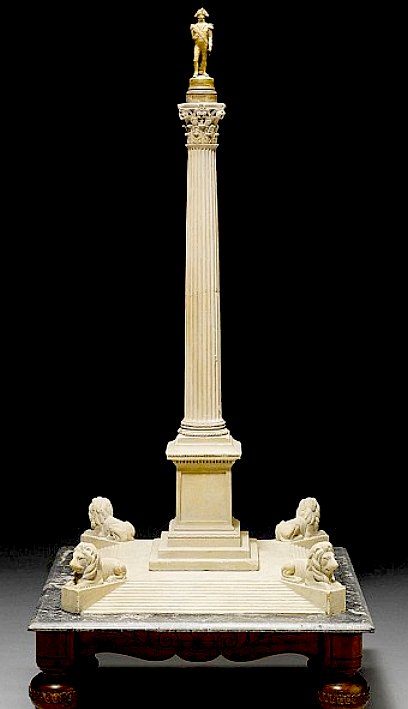
GETTING
TALLER - [Left] The steel column is seen here with the extendable inner
slotted in place. The ability to adjust the height is useful in
different locations where height restrictions may apply. The heavy
section steel and relatively wide footing makes this stand difficult to
overturn. That of course was one of the most important design
parameters: stability. The pedestal to column coupling reminds us of the
swash drive on the famous
Volkswagen
Beetle rear axle. If it was good enough for
Professor
Porsche, it's good enough for us. Interestingly, Ferdinand Porsche
was famous for battery electric vehicle before his air cooled boxer
engine for the people's car. He also used two front hub mounted
wheel-motors in the 14 horsepower 1889 Lohner-Porsche. He followed this
up with a four-wheel drive version that also had an IC
generator onboard to give us the first
electric/petrol
hybrid car. Now that is some serious innovation. Porsche would have
attended exhibitions
like Innovate2015. Does the stand remind you of anything?
SCALE
MODEL - [Right] A 1:50-scale stone model of Nelson's column,
made by
William Railton
(Auctioned at Bonhams Nov 2010), shows he had wanted a
magnificent edifice - 200ft tall, standing on a high, stepped pedestal,
guarded by four enormous, stone lions.
But the finished column was 30ft shorter because of budget cuts,
and initially, there was not a lion to be seen. Angry at what he saw as
the emasculation of his design, Railton refused to attend the official
unveiling
at Trafalgar Square in London in
1853 - and who can blame him.
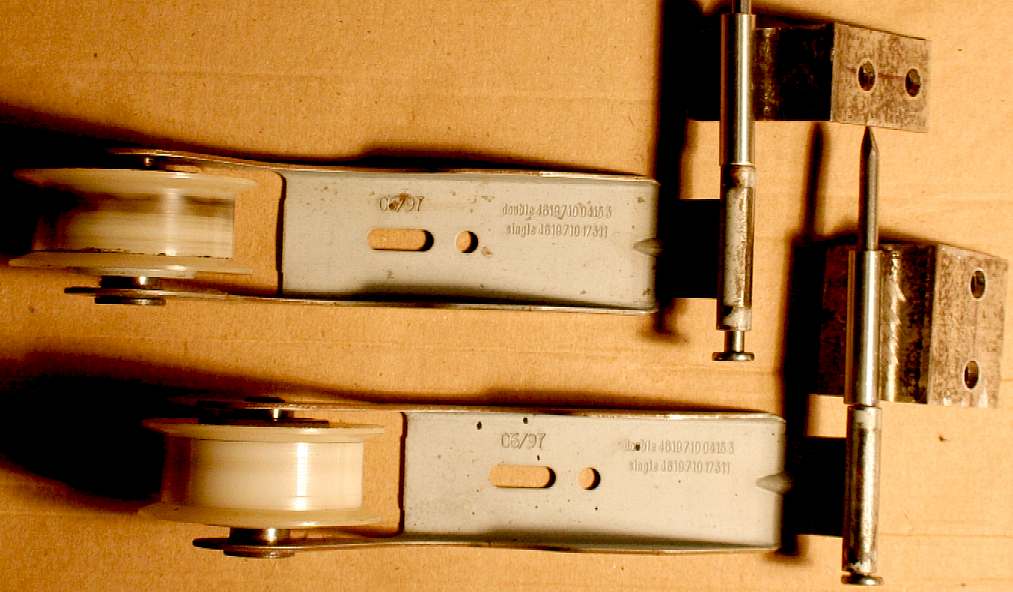
IDLERS
- These are ordinary tensioner assemblies as used in many domestic
tumble driers. The same width and ribbed 'V' section rubber belts are
used in these driers, only they are about twice the length. Isn't standardization
wonderful. That of course means that the pulleys are the correct width.
Nylon is used for the injection moulded wheels, that have sintered
bronze bushes running on superbly machined steel pins. The porous bronze
bushes holds enough lubricating oil for the life on these machines.
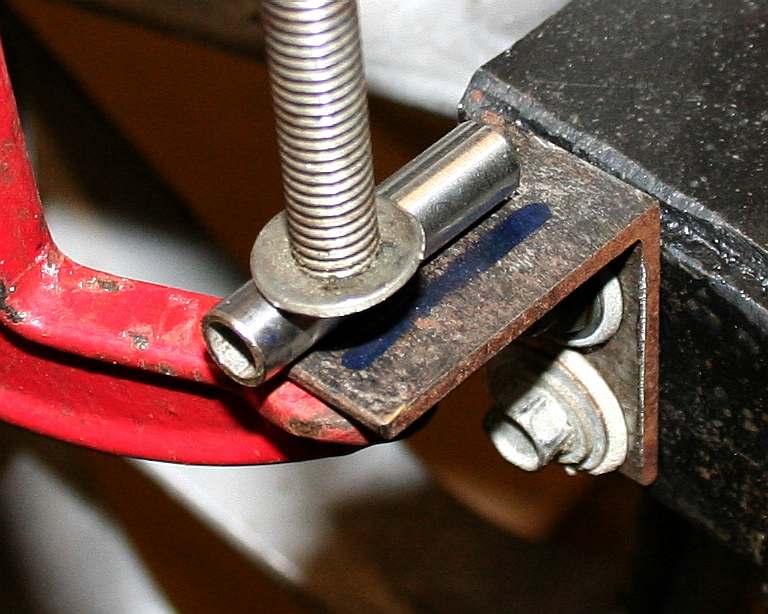
TENSION -
The mounting brackets for the spring loaded idler wheel that tension the
ribbed rubber drive belt. To save time we used proprietary self tapping
screws for these mountings. A steel tube is welded to the brackets and a
pin drops in from above - here simulated by a 3" nail - that is
unfortunately, too small in diameter to use. Dag-nabit. The steel tubes
are shown here jigged, ready to be welded to their respective brackets.
We'll be using around 70 amps for these welds, so as not to penetrate
the thinner wall tubing. Weld from the angle to the tube with the weld
pool, not the other way around.
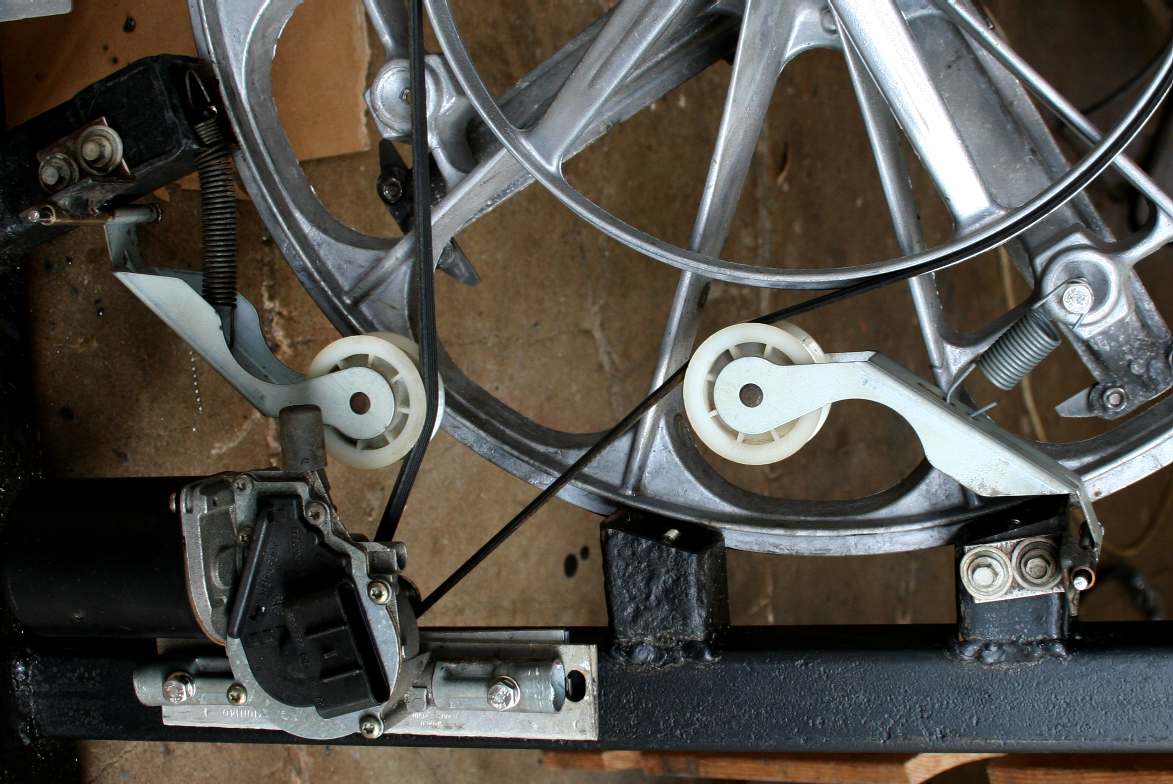
TENSIONERS
- The completed assembly working nicely. Now all we need is a couple of
split pins and some lubrication for the hinges.
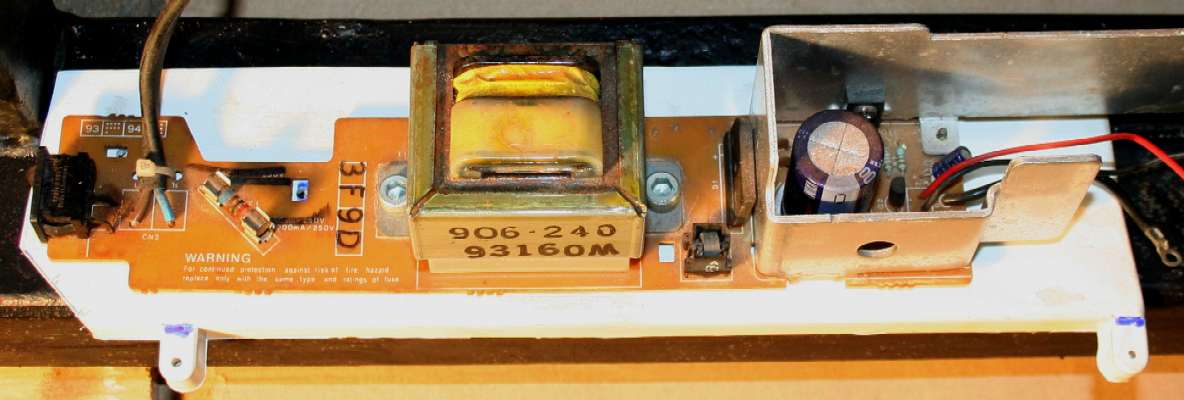
POWER
- This is a 400 watt step down transformer PCB scavenged from an old
stereo system, providing 5 and 12 volt outputs. The rectifier chip and
smoothing capacitors are seen to the right of the transformer. If at a
later date we decide to have speaker interaction and infra-red or other
motion detectors for human recognition, or tracking, we have the power source to cope - when the stand
will become a sort-of robotic interactive display (not for this show). The unit
was bolted to the underside of the main steel frame, with an insulating
plastic divider, The in-line layout is perfect for this installation. A
steel shield will cover the entire unit with additional heat sinks added
to dissipate any build up from constant operation. There is a convenient
on/off switch that can be located when in use by anyone who knows where
to feel, and a 3 amp safety fuse in the circuit. Provision will be made
to mount Arduino
and Raspberry
Pi boards. This display stand may one day form part of a permanent
exhibition
in Eastbourne,
so will need to be both robust and reliable.
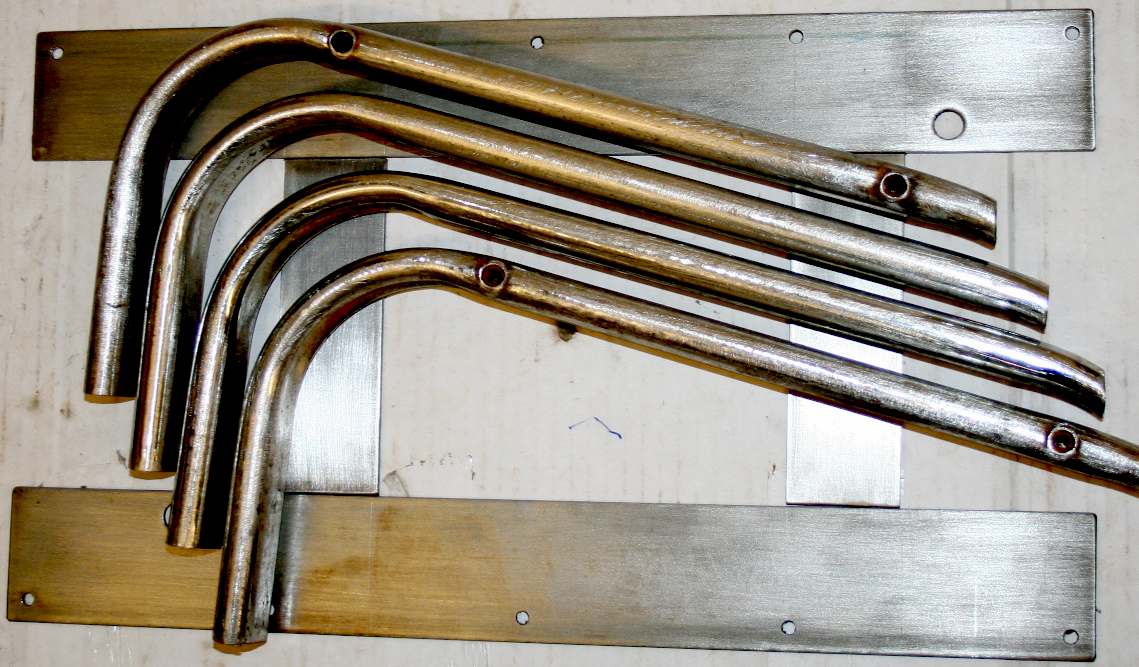
CRADLE
& MOUNTING BASE PLATE - This was the cutting list for October
5th. The flat plate is stainless steel, which can be a problem to drill
if you don't use sufficient cutting fluid and have sharp drills. 10
holes were drilled accurately so that the model can be mounted fore and
aft in increments of 95mm. 20 holes would have given 47.5mm adjustment
options, but taken longer to make. The two cradle frames are made from
old office chairs. The steel is surprisingly high quality seamless oval section.
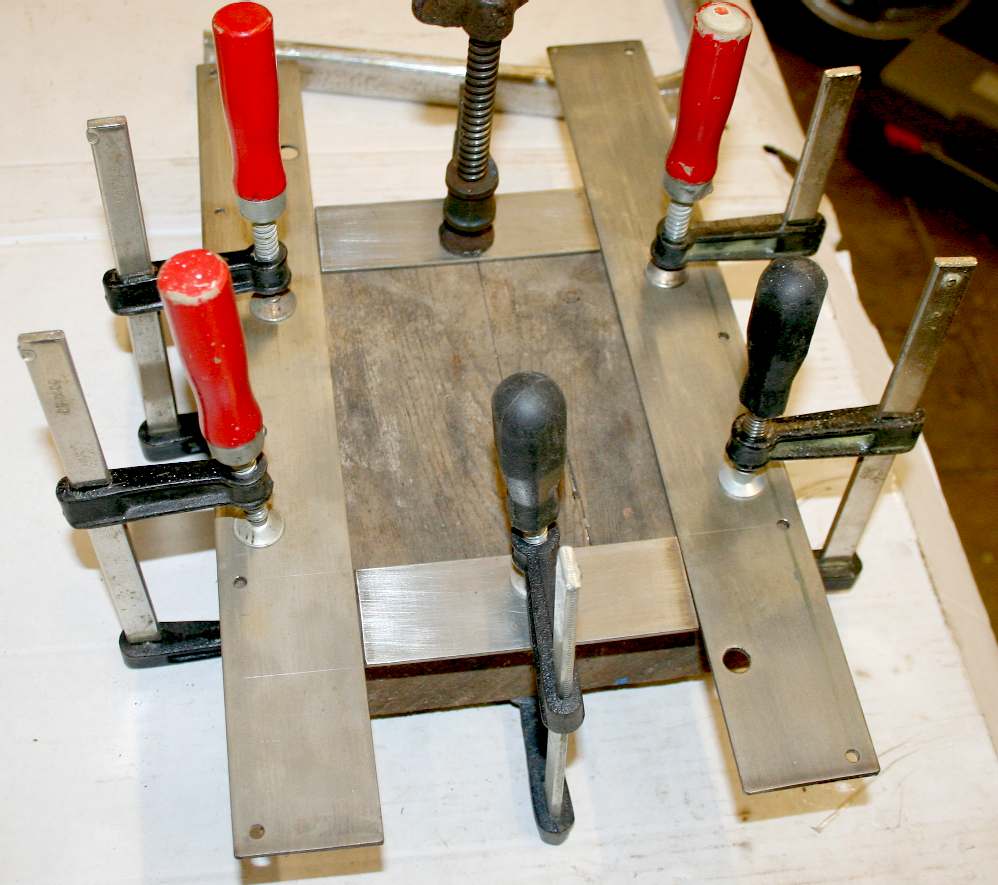
BASE
PLATE CLAMPING - Having marked out the plates with a scribe and beveled
the stainless steel ends to remove sharp edges and ensure weld
penetration, carefully line the frame up and clamp to a sturdy flat
object. Normally this would be steel, but here we've used a chunky piece
of wood. Even with this simple frame, weld sequence is important to
prevent distortion. We will tack weld in the 8 corners first, then weld
the flats together - again in a sequence to minimize distortion. Work
quickly when undoing the clamps and re-clamping for the reverse welds.
Check for distortion at each stage.
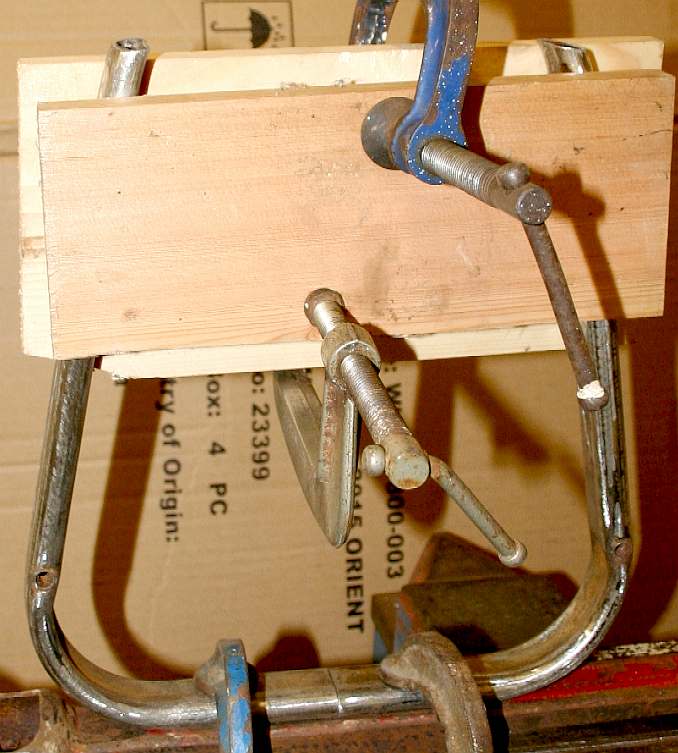
CRADLE
HOOP -
The cradle at the column upper end is clamped to a steel bar and the
upper arms clamped between two 1" planks of timber. Not ideal, but
accurate enough for hand construction, where minor fettling will ensure
a good fit. The tops of these cradle frames will be welded to the base
plate above, there are two of them. The base will be bolted to two
circular steel sections that form a swivel clamp that will allow change
of angle of the model display - simply by undoing a handle. The SeaVax
suction assembly will pass through this loop with clearance to spare.
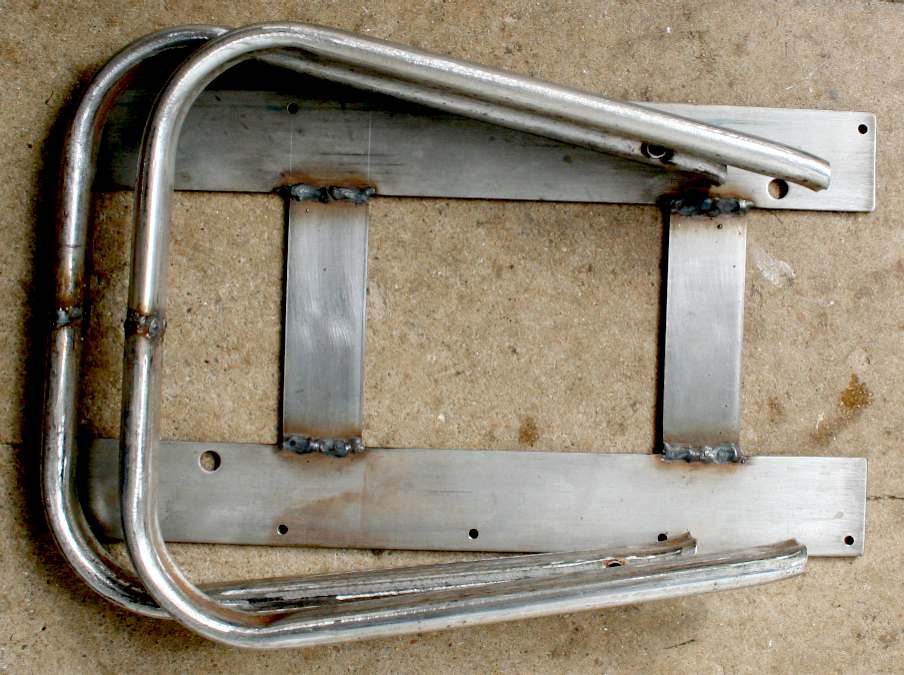
WELDED
- The cradle frames and base plate welded nicely distortion free.
Unfortunately, the method used to keep this plate flat means short
welds, hence the finish is less than attractive.
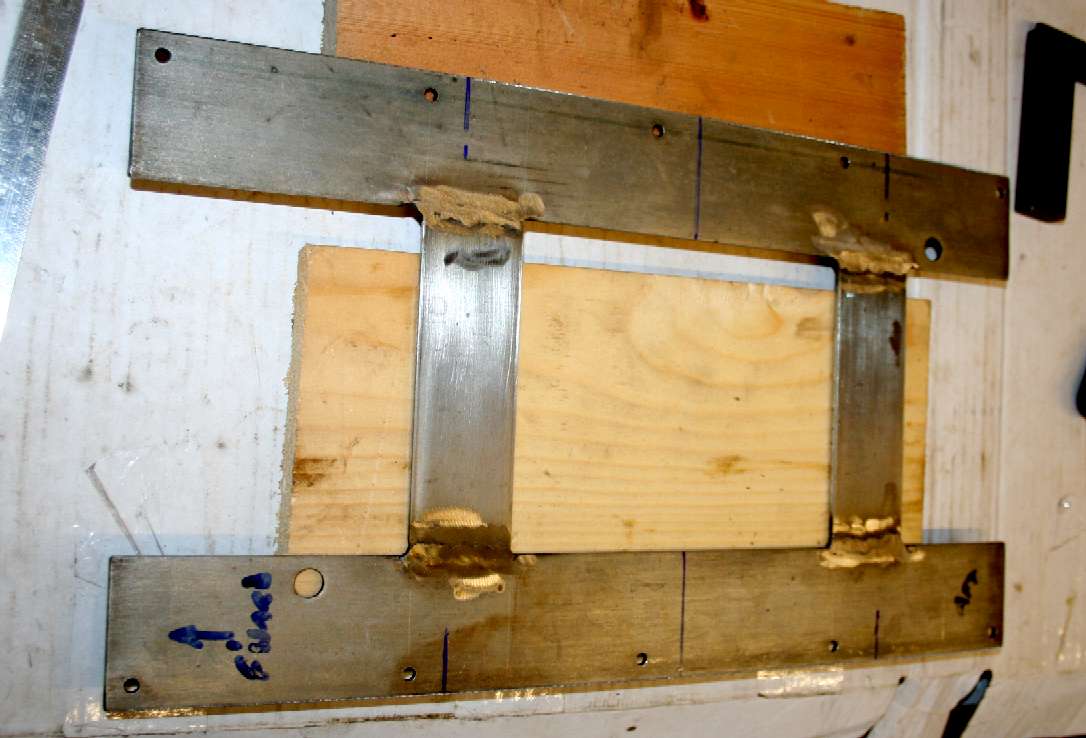
GROUND
BASE PLATE
- Grinding a weld weakens the joint. Sometimes though, there is no
option, as in this case. The base plate screws to the underside of the
deck of the SeaVax proof of concept model. It therefore has to be flat,
so as not to mark the boat. The plate is way over strength anyway,
especially as the weld is full penetration from both sides.
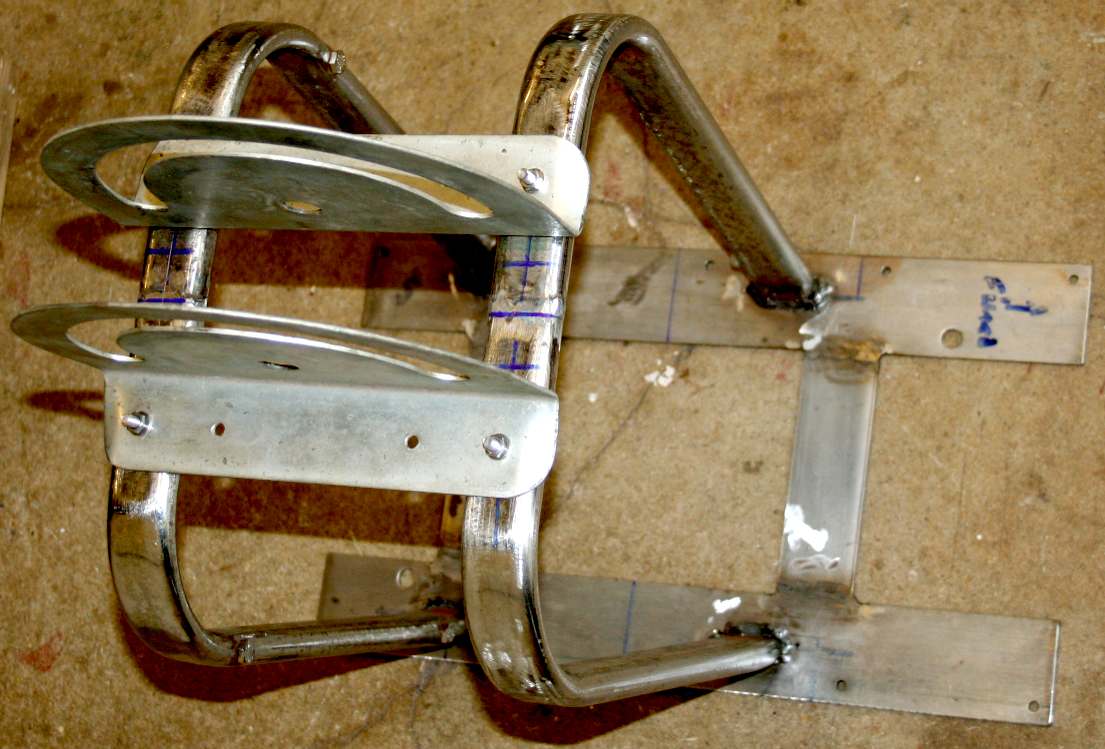
CRADLE
& SWIVEL ASSEMBLY - We use blue marker as a rough guide, with
scribed lines as the marks for punching and alignment. The swivel plates
are bolted to the cradle hoops. These small 6mm bolts were only used to
jig for welding. They will be replaced with some more manly 10mm items
before the SeaVax model is mounted. The cradle is a necessary
complication where it was not possible to mount the SeaVax on the
plastic treatment assembly that is suspended under the main deck of the
hull. That would have been asking too much of some relatively complex
machinery. Hence, the loads had to be taken around this obstacle,
which is also the most important part of a robotic vessel designed to
clean plastic from the oceans.
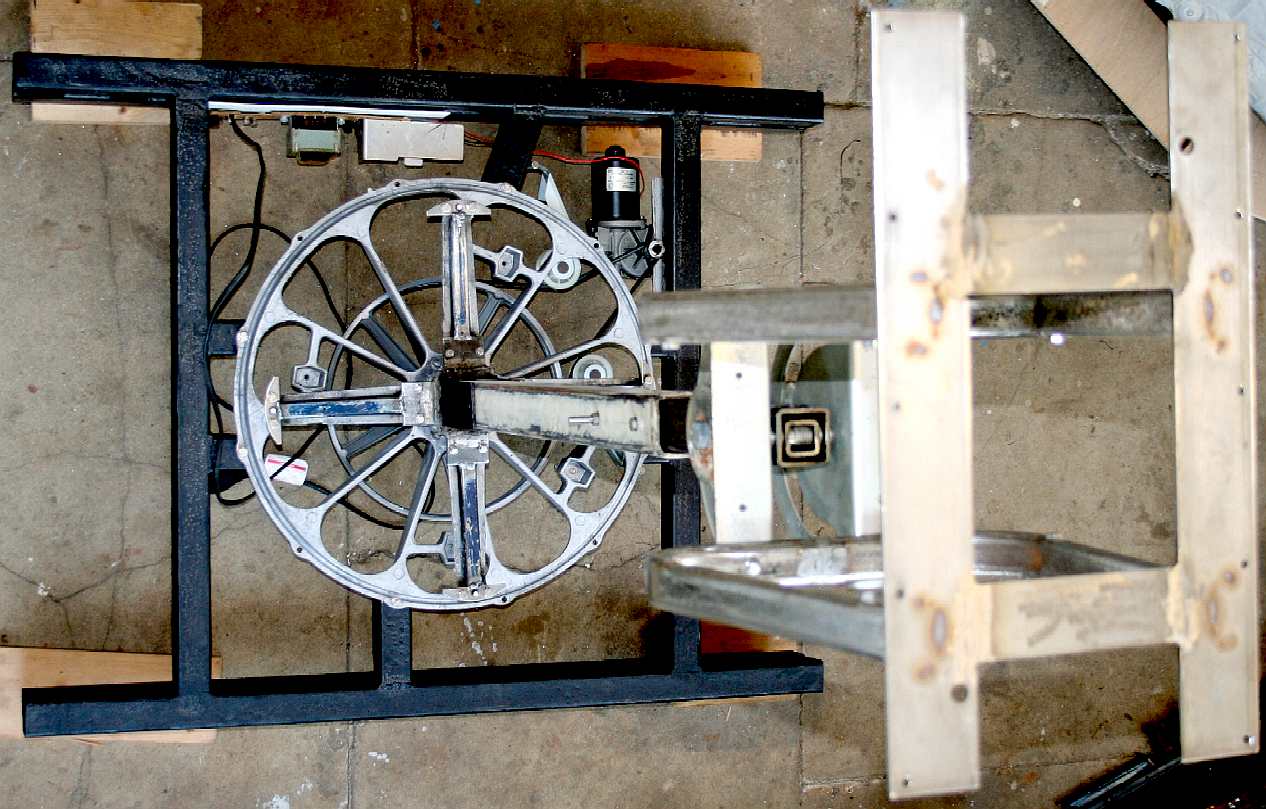
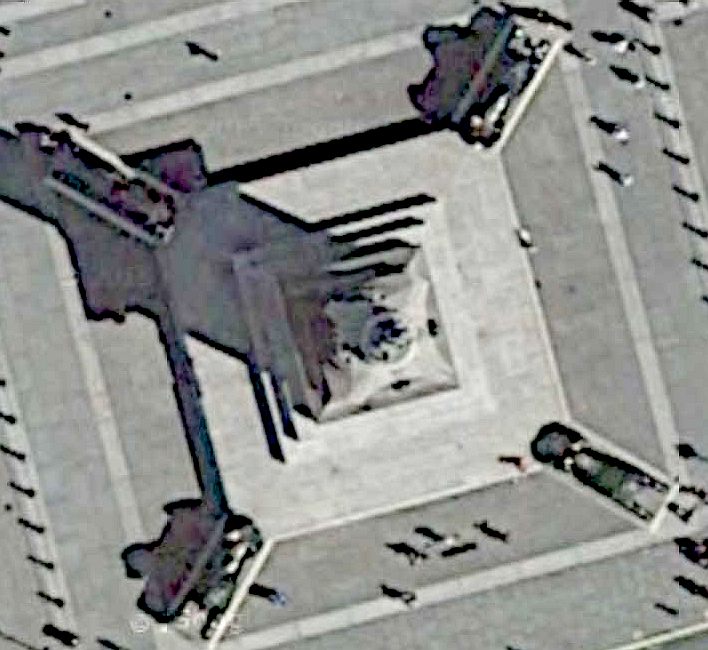
OBJECT
RECOGNITION - This is as close up as Google maps gets using their
satellite setting. In other regions the definition is better, as with
the street function. You can though see that the pedestal cross-trees
form the same shape as Nelson's Column, as with our show stand. Now all we need is a lion in each
corner. See more details of the pedestal below.
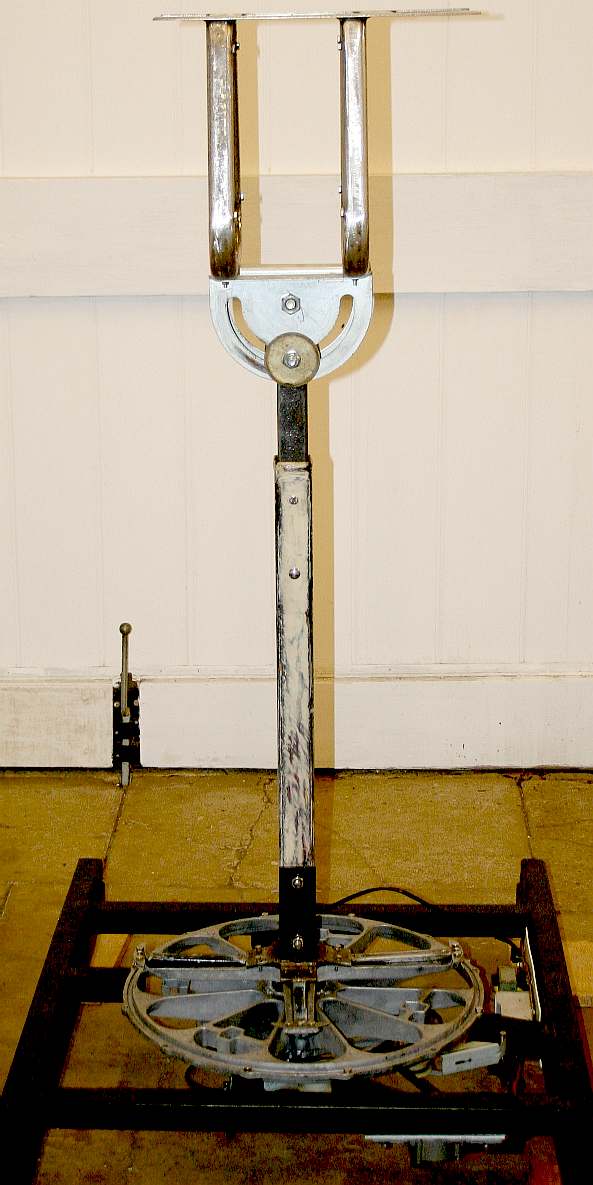
NELSON'S
COLUMN - October 8th: Okay, so Lord Nelson has been replaced
with the steel cradle mount, and please excuse the jaunty angle
of the
photo on the left, the cameraman was not focused. These are end
and side
views of the show stand before introducing any offset in the
inner
sliding shaft, that may not be necessary. The inner shaft can be
raised and lowered in 100mm
increments with four securing bolts from inner to outer, to keep
it rock
steady. An offset may be needed to keep the boat model's
rotation as close
to it's centre of gravity (and as near inline as possible with
the
column). Tilting the cradle without an offset (or dog leg) may
have the
effect of moving the SeaVax off-centre of rotation by up to
200mm and that is not the effect that we are after. A little trial and
error testing is next to obtain the best effect. The aesthetics
of this
cannot be appreciated on a drawing board - it has to be seen in
action.
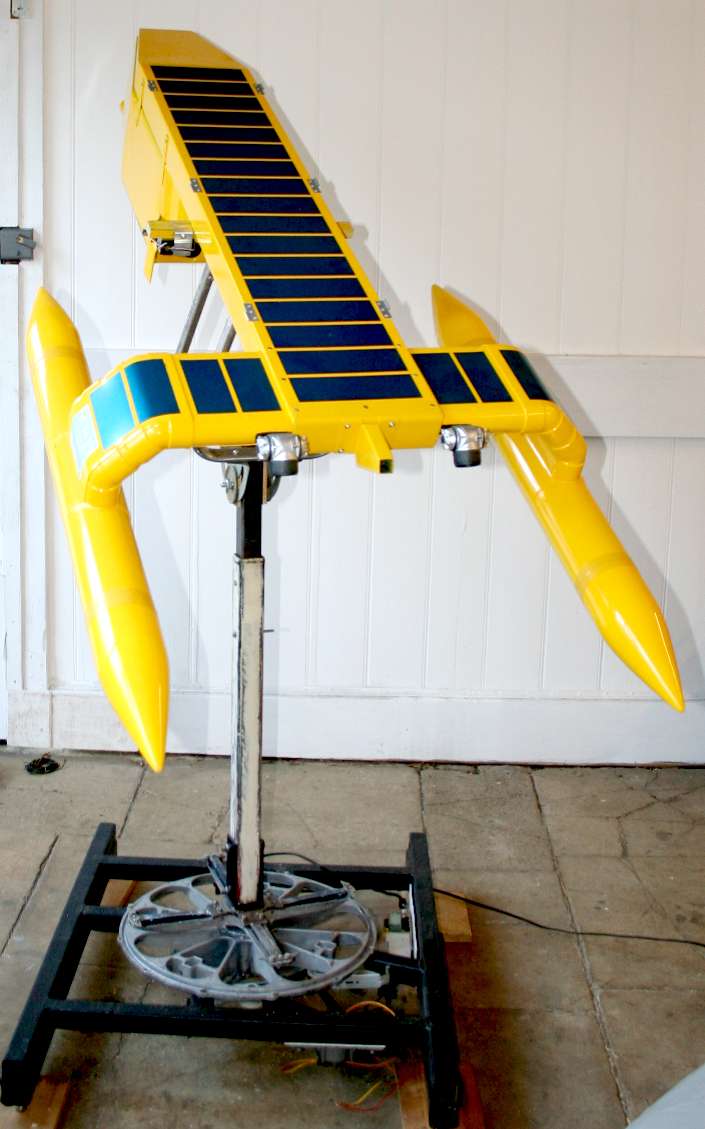
POETRY
IN MOTION - October 9th: The plinth and column will be painted white
for Innovate2015. The stand is rock-solid even at this angle and at any
point of the rotation cycle. The clamp works like a disc brake on the
steel swivel. Our friction (brake) pads are cut from 9mm hardwood ply,
rather than the cellulose, aramid, polyacrylonitrile (PAN) and sintered glass
composites that are used for car disc brakes, sometimes with a
sprinkling of metal (copper) flakes and even clay and porcelain in the
mix. The motor drive purrs as it powers the circular plinth at between a
half and two-thirds of a revolution per minute.
For
any interactive display use we may include a variable speed controller,
that the rotation speed can be much higher. We might also replace the
four circular pads with low-profile motorised wheels, so that the stand
can be driven, or appear to follow visitors. Not though at Innovate
2015. Lastly, the tilt mechanism can be motorised, turning this
innocuous stand into a Johnny
No 5 like machine - simple fun for youngsters who might be inspired
to one day build innovative
robots
themselves.
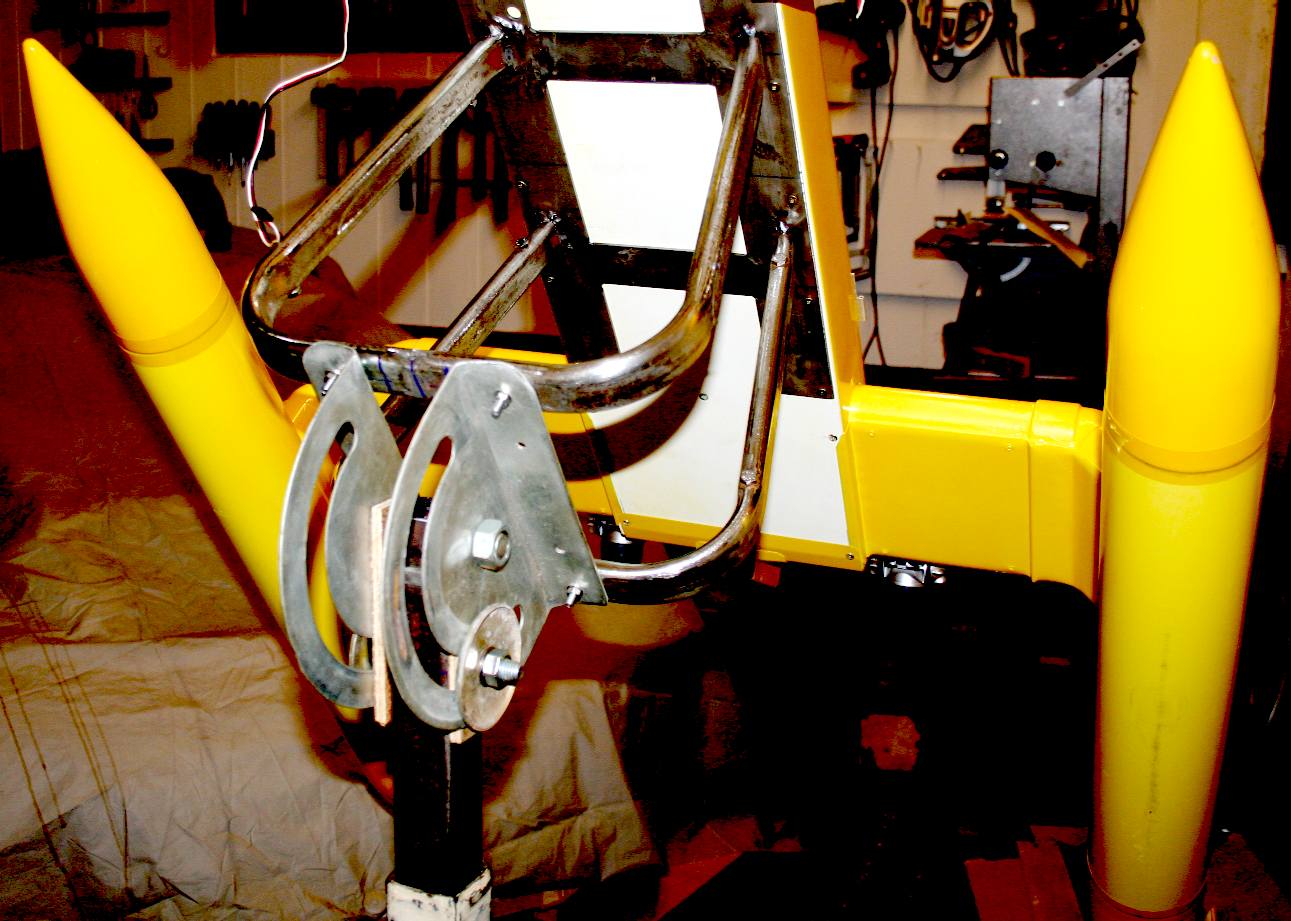
ANGULAR
ADJUSTMENT - This example of recycling is a good reason not to throw everything away.
In fact, somehow, having a few bits and bobs lying around seems to
stimulate the mind when it comes to ad hoc fabrication. Improvise for
all you are worth and help us to save planet earth. We plan to motorize
this function for displays in 2016. The movement will not be all that
different from some cinema quality camera pods or even missile
turrets.
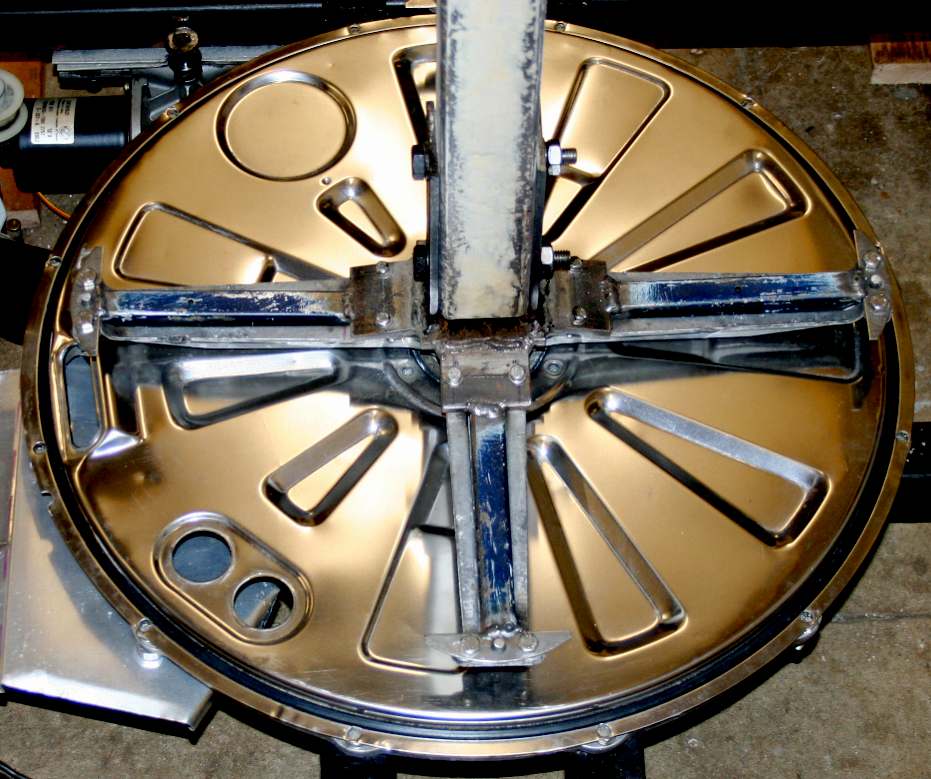
PEDESTAL
- Left: This plywood base bolts to the pedestal cross-tree seen on the
right. It will be sealed and painted in white to match other plywood
panels (not shown) and the steel frame and column upright. Below this is
a stainless steel cover with vent and service openings. You can see the
aluminium heat sink below the vent (bottom left).
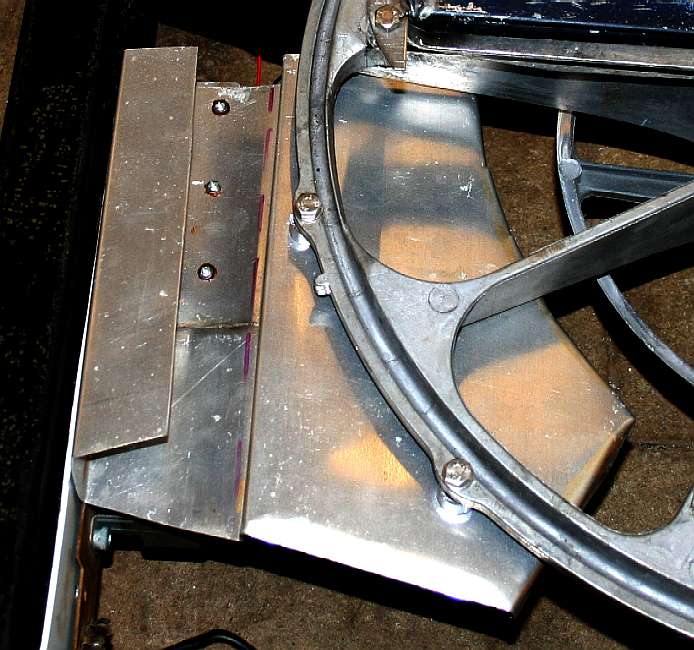
HEAT
SINK - Where the power demand is more sustained than with an audio
amplifier, we have added a substantial aluminium heat sink. This is
bolted to the bearing spider and the smaller PCB mounted heat sink using
plenty of heat transfer grease. With heat sinking (heat dissipation),
volume and surface area are important, as is airflow. A good example of
this is the VW
air cooled boxer engine, except that the cylinder finning on that engine
is cast iron.
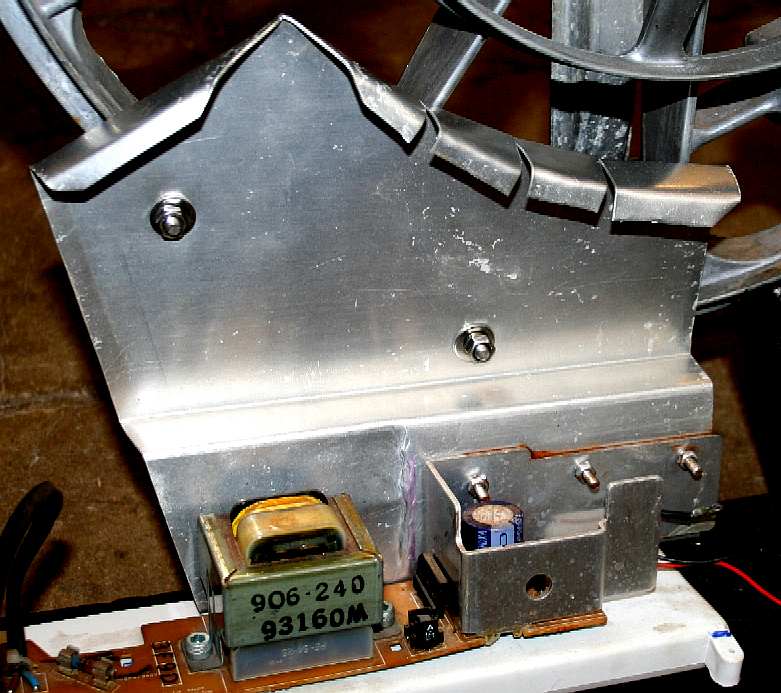
POWER
ELECTRONICS - This is the underside view of the heat sink which
doubles up nicely as a water splash cover for the electrics. In service,
reliable operation is crucial. Electronics that operate cool last
longer, the same applies to motors. We can switch to a battery back up
in the event of a power failure, or there being no power supply at
road-show type mobile venues. While not in use the batteries are trickle
charged. If solar panels are added, the whole display could operate more
or less continuously from natural sunlight, just like the SeaVax vessel
that is being displayed.
LEAD
ACID (AGM) BATTERY - Four of these Powerline 12 volt lead-acid
batteries
will power the stand off grid for an 8 hour duration. They are
the
perfect size to fit in the base. Lithium polymer batteries could
also do
the same job. See the equivalents in the picture below. The
Powerline
batteries use Absorbent Glass Mat, or AGM technology, popular in
the early 1980s as a sealed
unit for military aircraft, and Uninterruptible Power Supplies
(UPS). The acid is absorbed by a
fine fiberglass mat, making the battery spill-proof. This
enables shipment without hazardous material restrictions.
Because of good performance at cold temperatures AGM batteries
are also used for marine, motor home and robotic applications. They
can be mounted at any angle.
LITHIUM
ION BATTERY - Compare the JMT 12 volt units (centre red) to the
Powerlines on the left. They use the latest LiFePO4 technology. Four of
these batteries weigh just 1.6 kilograms, or 3.52 pounds. That is
considerably lighter than the Powerline setup, but cost around four
times the lead-acids. The blue LiPO units also offer the same output as
the JMT units, but with with mains charging from a supplied adapter that
is very much smaller.
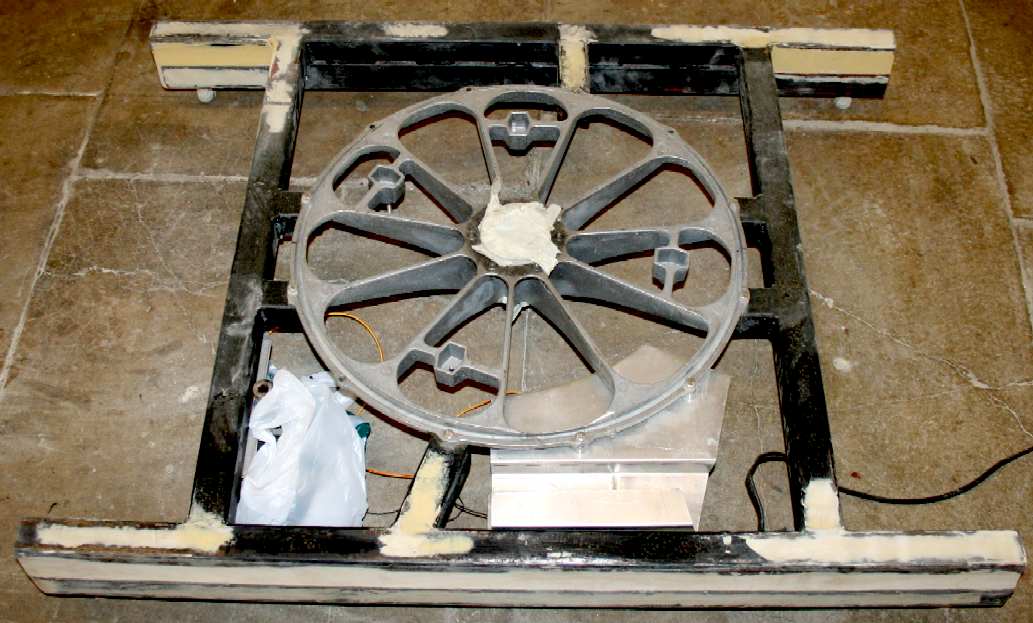
SURFACE
PREPARATION - Before painting any metal surface it has to be
suitably primed and sound. That means removing loose of flaking paint,
applying rust prevention treatments and where needed, other surface
preparations, such as filling imperfections with polyester filler. Be sure to mask any sensitive moving parts before
beginning these works.
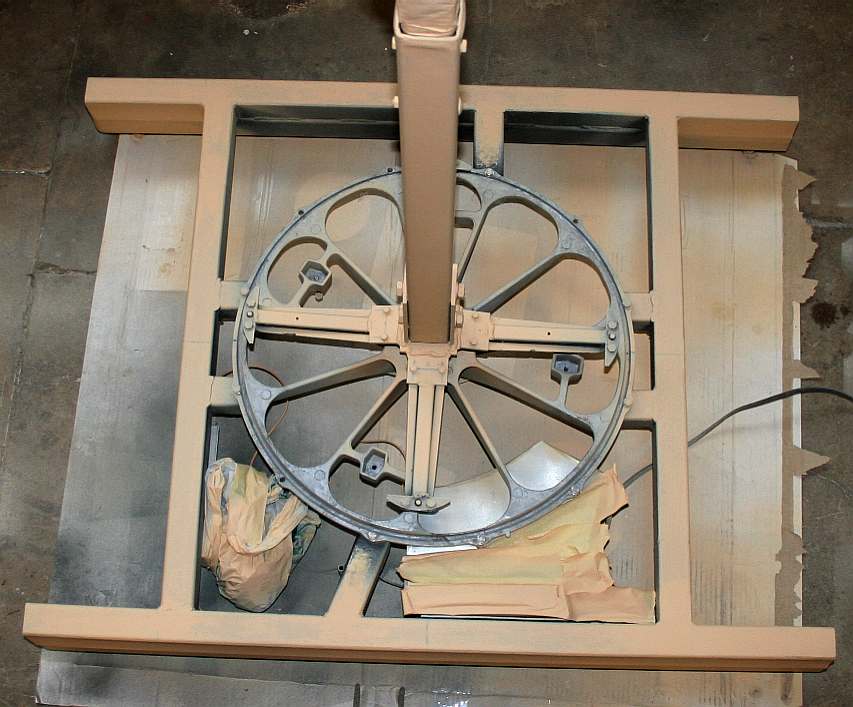
PRIMING
- Priming in the world of spray painting is also the undercoat. More
correctly, the primer paint is also a filler to smooth small
imperfections, sanding scratches and level the surface being painted so
that it is flat.
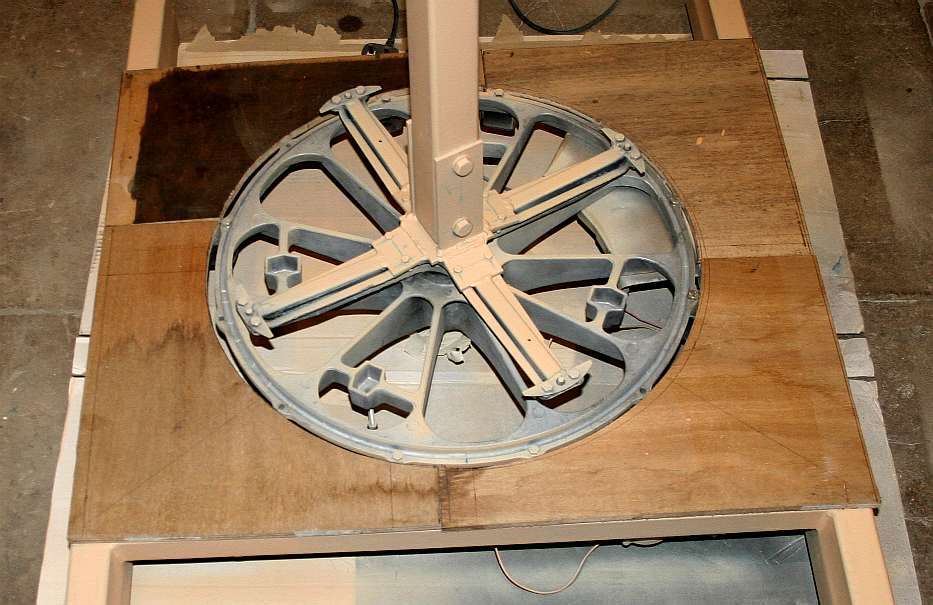
WOODEN
FLOOR PANELS - The stand needs a floor in the four corners. We are
using 11mm plywood for this. Each panel needs to be detachable for
servicing. The wood will be sealed, primed and painted the same white
and the rest of the plinth. The panels are not fully cut to size or
trimmed in the picture above.
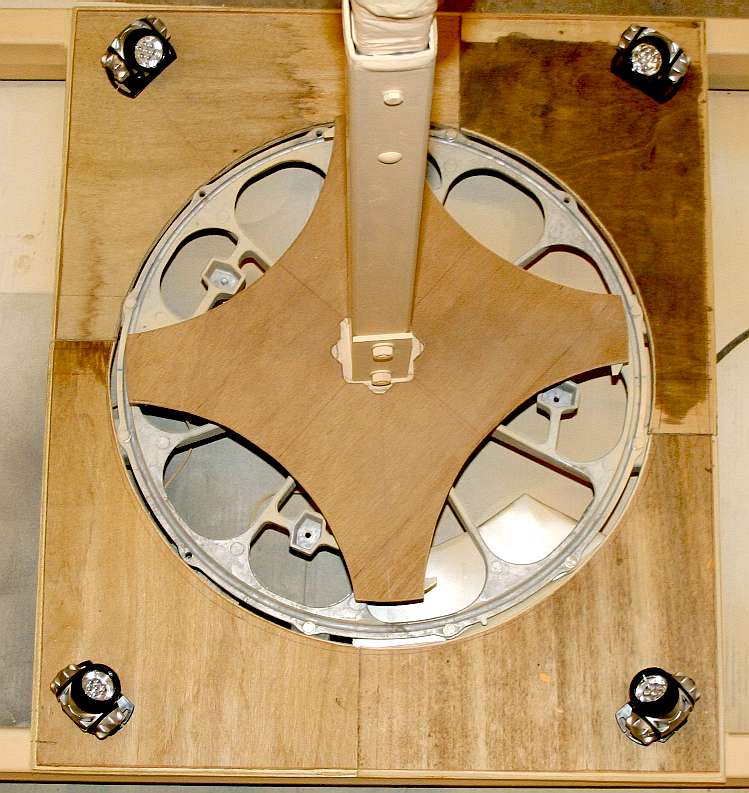
LIGHTING
- The floor panels are beginning to take shape with beveling to the
edges. The next step is to screw the panels to the steel frame for final
trimming. Four LED lamps have been placed in each corner to try out
potential angles for best effect. The revolving plywood pedestal proves
to be too small. We will keep this for reference.
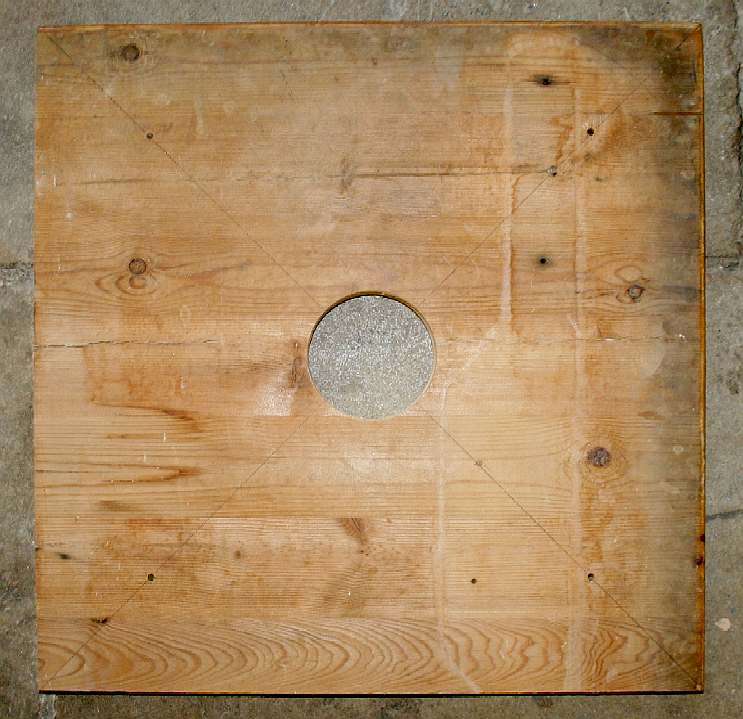
SHIVER
ME TIMBERS - A larger plank of wood is selected to sculpt another
revolving pedestal base. This is an important component of the display,
where timing of lights and more can be from each revolution with certain
triggers, mechanical, magnetic or optical. The timber is part of an old pine kitchen
table-top (off cut) that is around forty years old - and had been
kicking about the workshop for at least twenty years looking for a home. After marking out, the centre hole is
cut first.
RECYCLING
IN ACTION - Four holes are drilled to match the spider cross-tree radians. The
pedestal is bolted to the steel cross-tree below to check for alignment.
This pedestal timber is more robust than the previous plywood version.
It can accept a deep bevel. The great thing about wood is that it is a
renewable building resource, that also locks up
carbon
dioxide. Pound for pound, wood is
stronger than steel in certain applications but is harder to join.
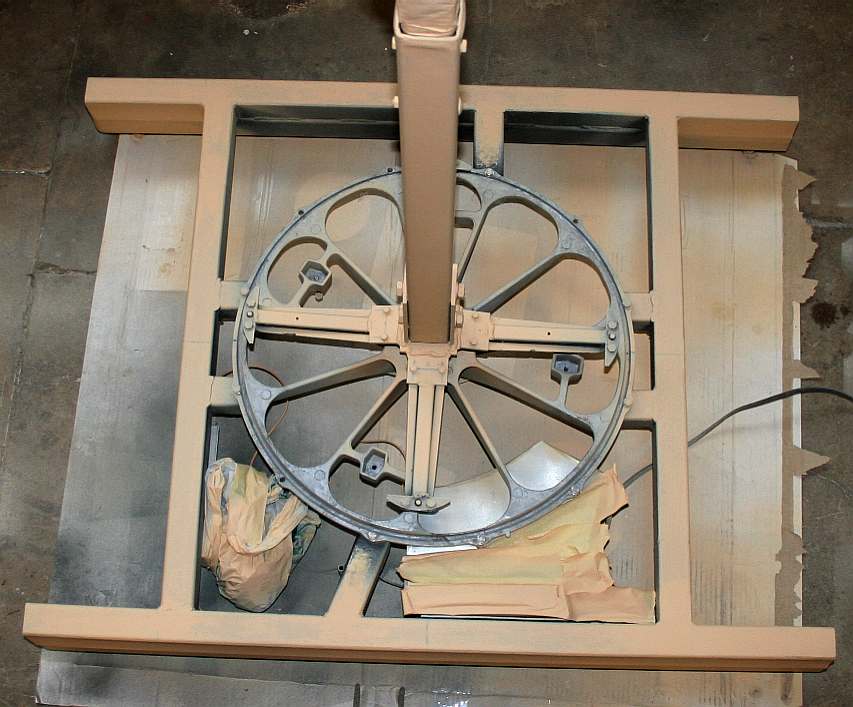
PRIMING
- Priming in the world of spray painting is also the undercoat. More
correctly, the primer paint is also a filler to smooth small
imperfections, sanding scratches and level the surface being painted so
that it is flat.
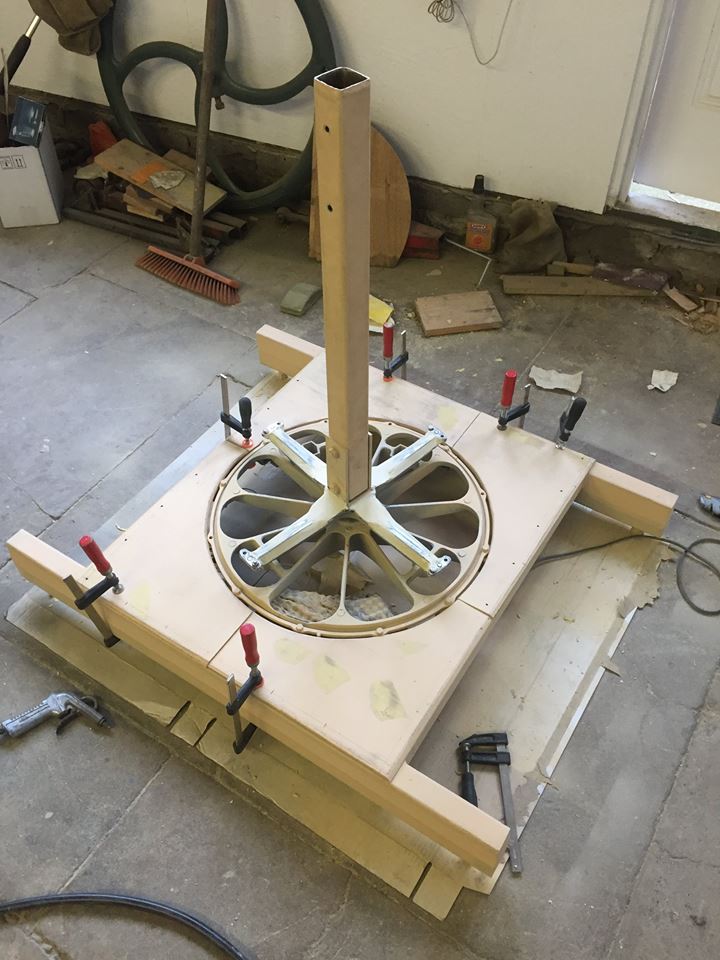
FIXING
WOODEN
FLOOR PANELS - The four separate plywood panels are fixed by
clamping them onto the steel base frame. The panels must fit exactly and
be chamfered and then holes drilled in a regular pattern through and
into the steel box section. Those holes are then tapped to accept
hardened self tapping type screws, since they will not need to be
removed and are simply fixings.
BOXING
THE COMPASS - The wood is primed at this stage simply to seal the
grain. Note that the revolving pedestal is now beveled. The panels are not yet
fixed. What a difference a coat of paint makes. Four miniature spot
lamps are positioned in each corner of the plinth: North, South, East
and West. They will be mounted on suitably styled blocks and also be painted
white to match the base. Horatio Nelson's statue faces towards the famous
battle where he made the ultimate sacrifice: Trafalgar. The square
represents a symbolic compass for the naval hero. These days a compass
is largely redundant where GPS is the norm, but basic navigation skills
should be part of any sailors training.
LIGHTING
- The standard LEDs in these lamps may need to be upgraded. The
stainless steel shield below protects the bearings and provides cooling
ventilation for the electrics. A clutching system stops rotation of the
show model at the
slightest touch.
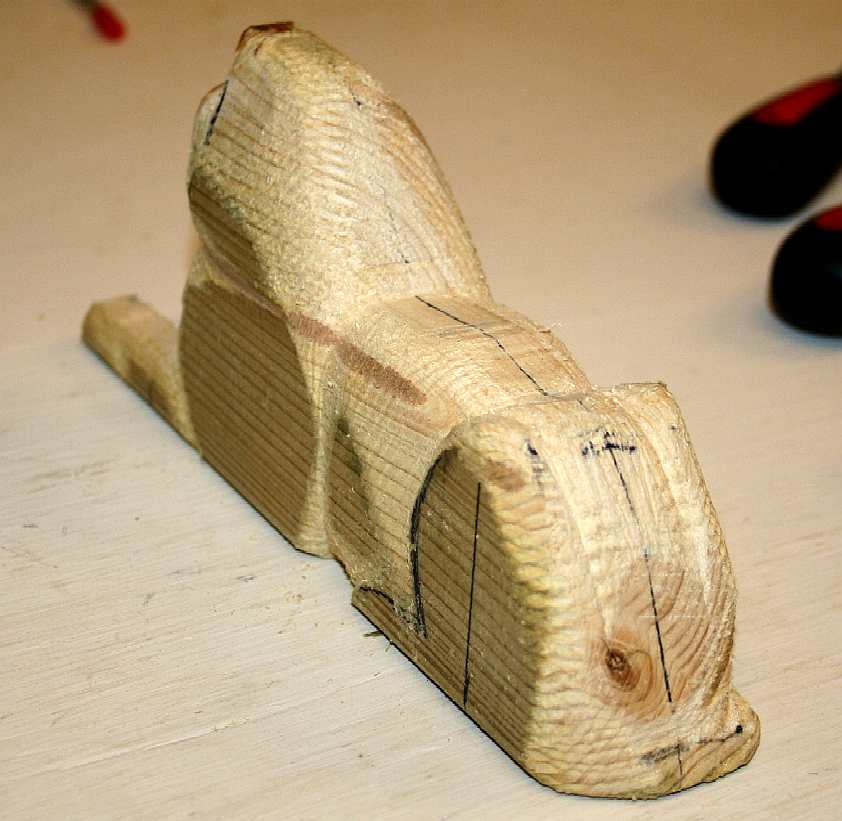
SIR
EDWIN LANDSEER - On the theme of Trafalgar Square, Nelson's Column
has four lions on the base that
symbolically guard each corner of the Empire's compass.
In 1858 the British
government commissioned Sir Edwin Henry Landseer to make four 22 foot bronze
lions for the steps of Nelson's Column. Our artist decided to have a look at carving a simplified
version of Landseer's splendid works from a wooden block - at a scale
suitable for our show stand. The time allotted for completion was half a
day (4 hours). The team have
not decided to incorporate the lions, it is just an art exercise at
the time of writing using photographs of the lions that Sir Edwin carved
as inspiration. Landseer is famous for his anthropomorphic artworks and
the Monarch of the Glen painting of a Highland stag. See how to carve a
lion like this by clicking on the picture above. These same skills are
needed for making ship figure
heads, along with a sharp
set of chisels.
PLYWOOD
DECKING - October 25 - The compass deck (or dial) is comprised of
four panels that are screwed to the steel box section with no less than
30 hardened steel fixings. The deck is sealed with cellulose high build
primer/filler, with re-cut bevel edges, but will need more fettling to
get rid of surface imperfections before spray applying a white
undercoat. The cross-tree ends have been trimmed, shaped and sanded.
This gives us two versions of the stand, one for naval
and boat shows, where the Trafalgar Square tribute will be appreciated
and the other for technology events, leaning more to robotics. We may
carve a scale version of Admiral Horatio Nelson to replace the cradle,
should any organisation wish to hire this stand in relation to any
historical or naval events.
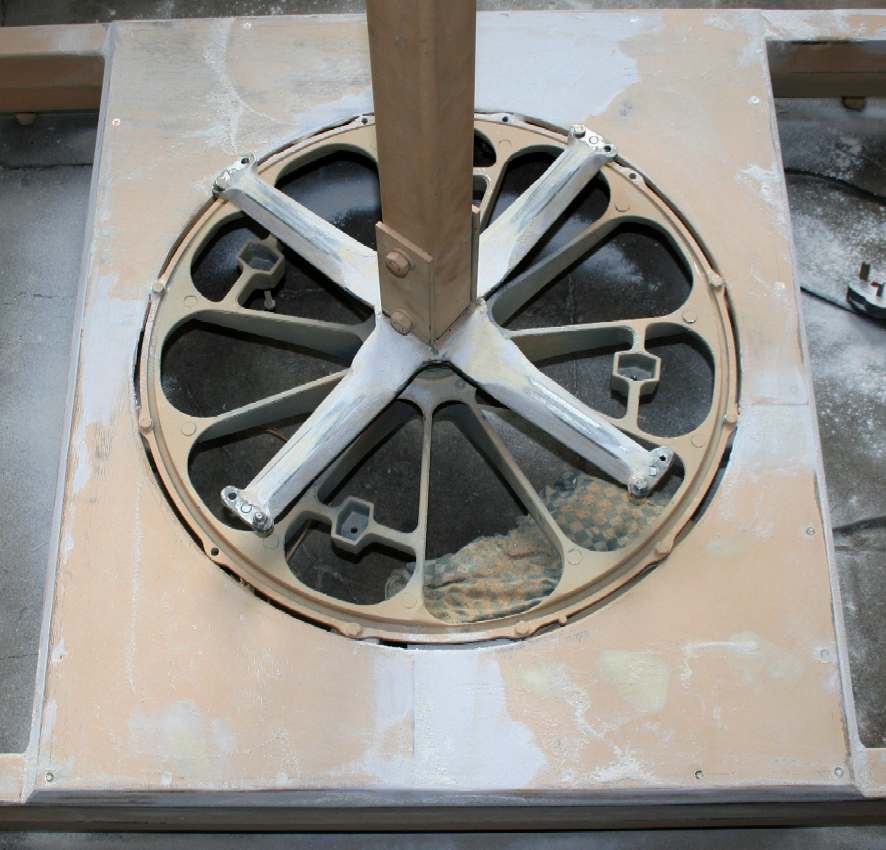
SURFACE
FILLING - Once fixed in place it is then possible to fine surface
prepare for a white undercoat. Different colour primers and fillers
allow the spray painter to see imperfections such as chips and scratches
more easily as he progresses. Wear a mask so as not to breath in the
dust.
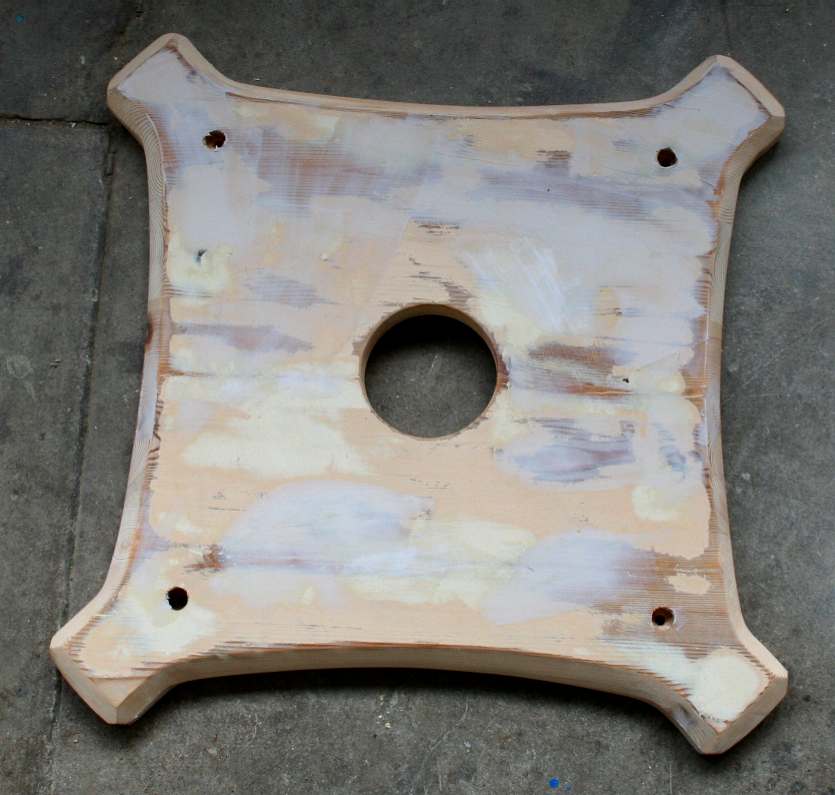
TRAFALGAR
SQUARE - The revolving base for Nelson's Column is fine surface
filled. It will take more primer/filler coats and end grain sealing
before we can apply a topcoat. As a natural material, wood needs a deal
more surface preparation than metal, where metal parts are man-made and
so relatively uniform. Wood has knots and grain to deal with.
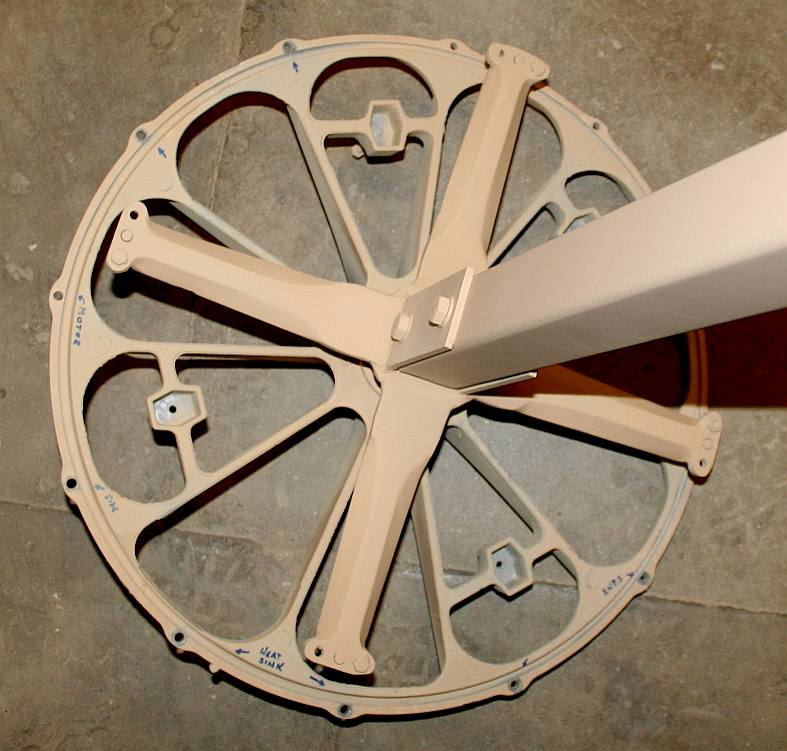
SPIDER
- The spider-web bearing mount is removed from the stand assembly to
prime and paint the cross-tree, otherwise it would be difficult to reach
under the radians. This piece of machinery has a very Victorian look
about it.
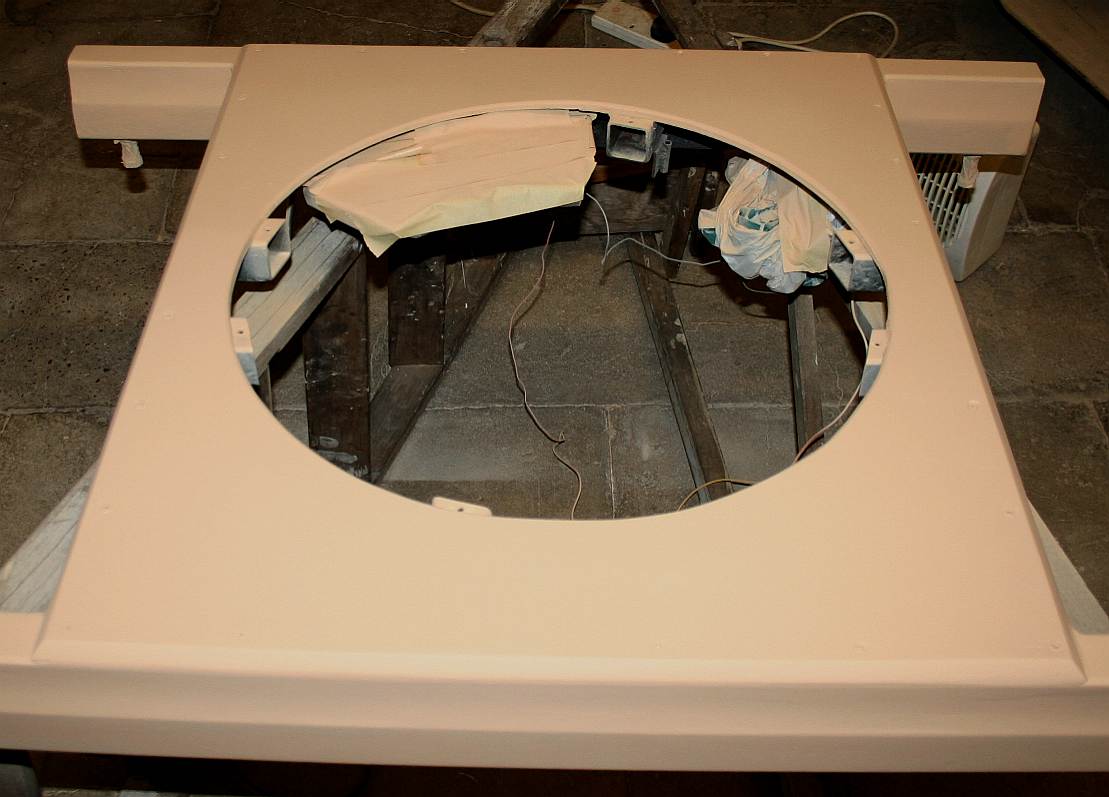
STAND
BASE PRIMER - Oct 26. Looking a little empty, the stand is primed again,
but will still need a micro fill to catch small blemishes and yet
another fine sand, before applying the white undercoat. Use production
paper 80 and 120 grit. There is no need to go finer for the white
undercoat, but the white will need a fine sand using 240 grit before applying the
2-pack white gloss, or topcoat.
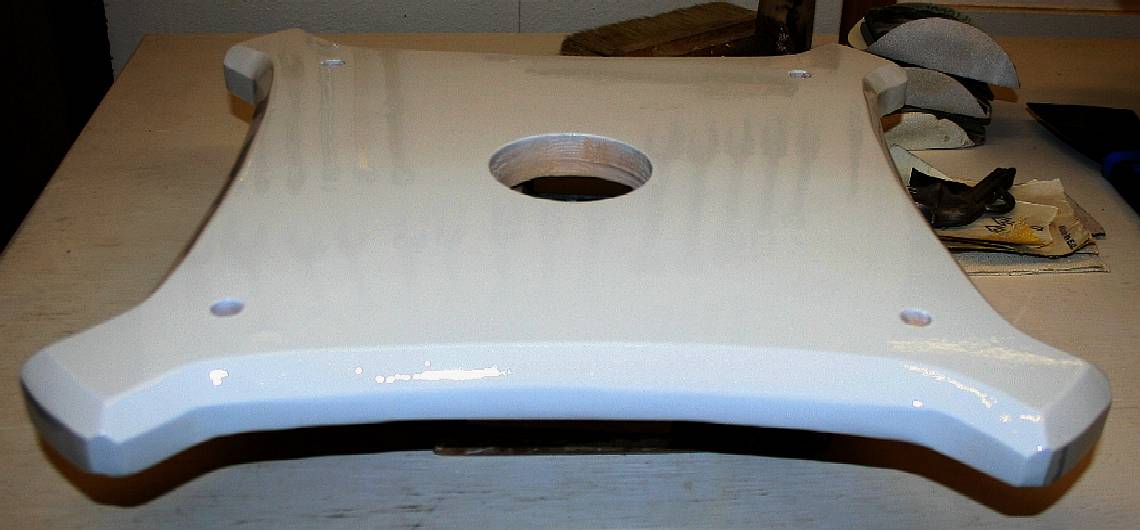
TRAFALGAR
SQUARE REVOLVING BASE 2-PACK - Oct 29. The base of Nelson's Column
is seen here with two coats of a good quality 2-pack paint. 2-pack
paints are dangerous if the correct breathing apparatus is not used. We
have extractor fans built into our roof that vent outside and even then
it was not advisable to remain in the paint shop until the dust had
settled. 2-pack contains cyanide. Interestingly, it was arsenic
poisoning that contributed to the death of Napoleon
Bonaparte, where the arsenic was a
component part of the green paint in his house on Saint Helena.
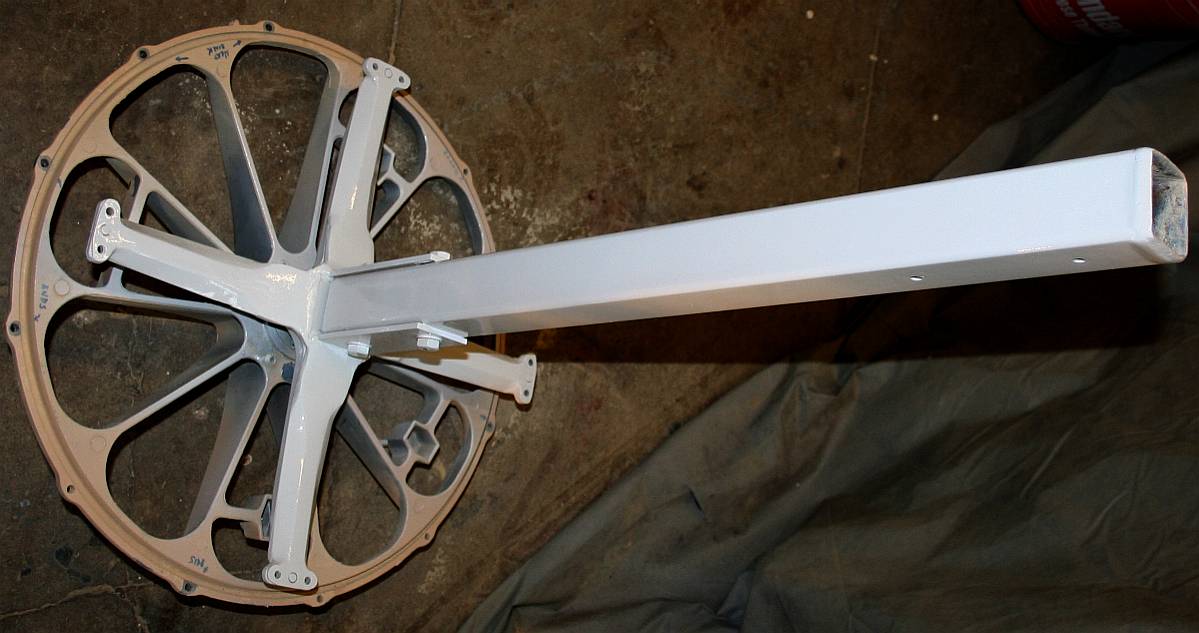
NELSON'S
COLUMN 2-PACK - Oct 29. As mentioned above, we have two exhibition
options, meaning that the cross-trees can be on display with or without
the revolving base for a Trafalgar Square theme. The show begins in 11
days time, when we deliver this stand to Old Billingsgate. We are booked
to set up our display on Sunday the 8th of November.
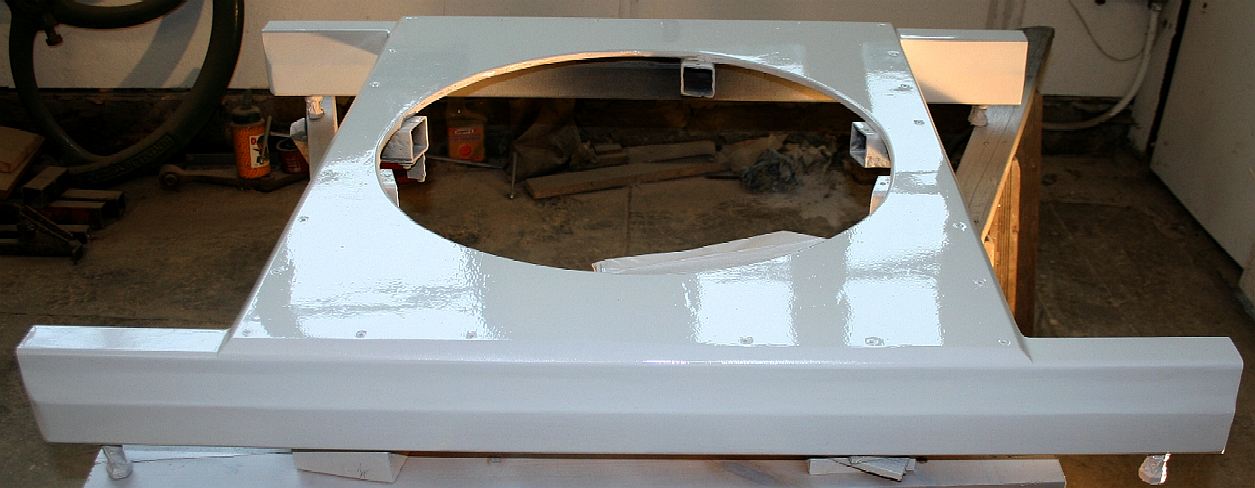
TRAFALGAR
SQUARE 2-PACK - Oct 29. Our spray painter had a bit of trouble with
the gun not delivering the right paint to air ratio. This was down to a
partially blocked nozzle. Spray guns frequently go unused for years at a
time. Be sure then to clean your equipment thoroughly after use and
before putting into storage. Now
comes re-assembly; the fun part. Prudence dictates that we leave the
paint to harden overnight - even though 2-part paints cure chemically
very quickly, rather than simply air dry - so are ready to be handled
immediately after baking in an oven, when painting a car for example. We
do not have an oven. We just put some lamps on the work pieces for an
hour, to keep them warm during cure.
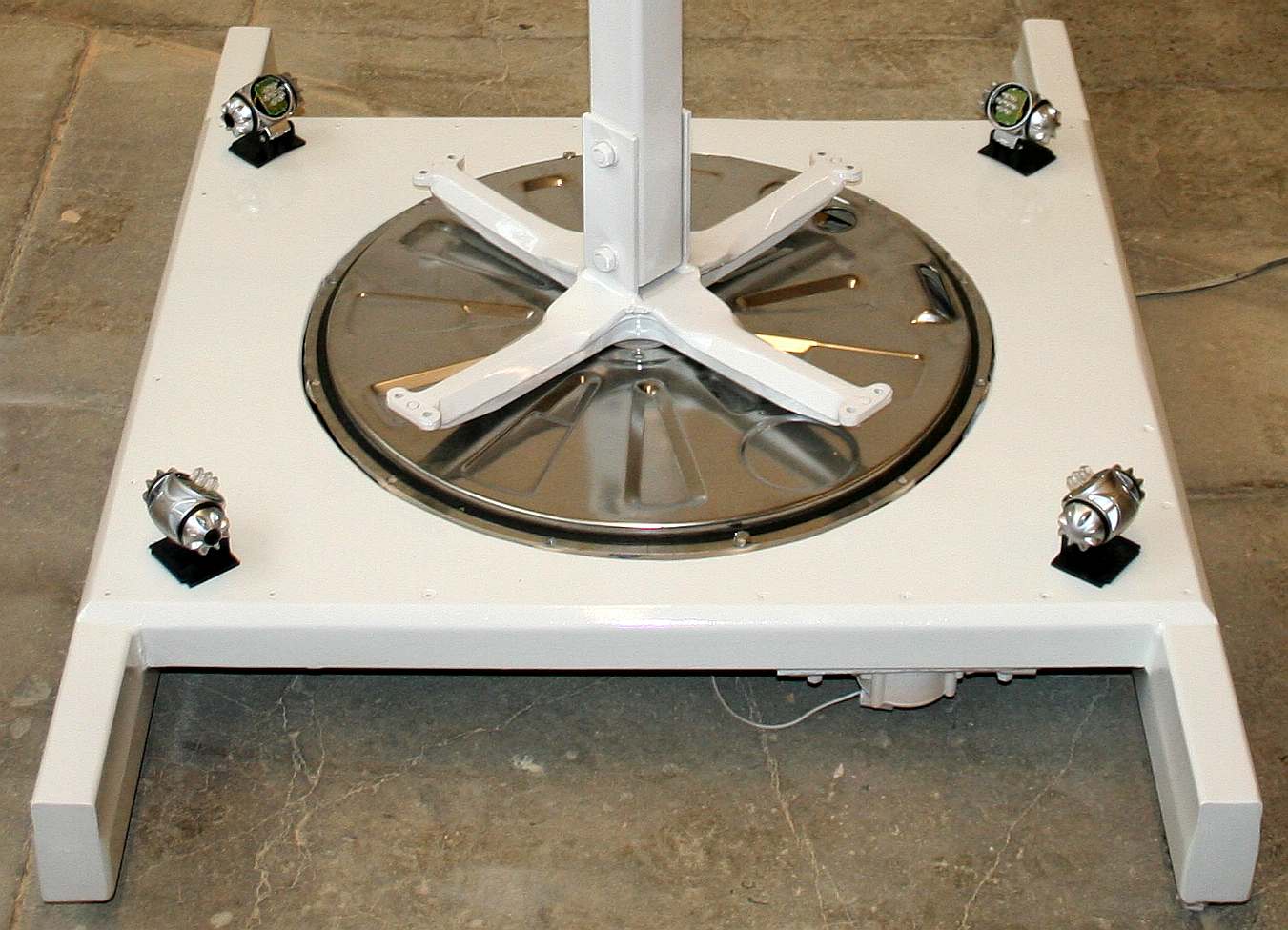
LIGHTING
- Oct 29. It's time to reassemble all of the painted components and wire
up the lights. LEDs hold the potential to save huge amounts of energy
for planet
earth, where they are so much more efficient that
Thomas
Edison's (and Joseph Swan's) incandescent light bulbs.
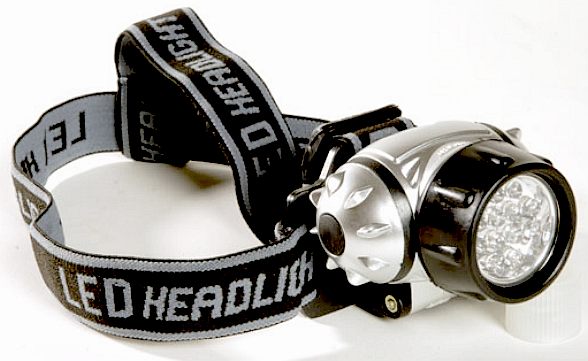
SPOT
LAMPS - These housings are used by many manufacturers for their LED
head torches. They are convenient for us and easy to modify. Use the
cheaper versions with 7 LEDs to experiment with and upgrade the light element to 12
LEDs, or even a car headlight unit, if you really want some punch, but
be careful not to go overboard - because the power pack will need to be
that much bigger. We use the same units on our proof of
concept vessel to house infra-red and other sensors.
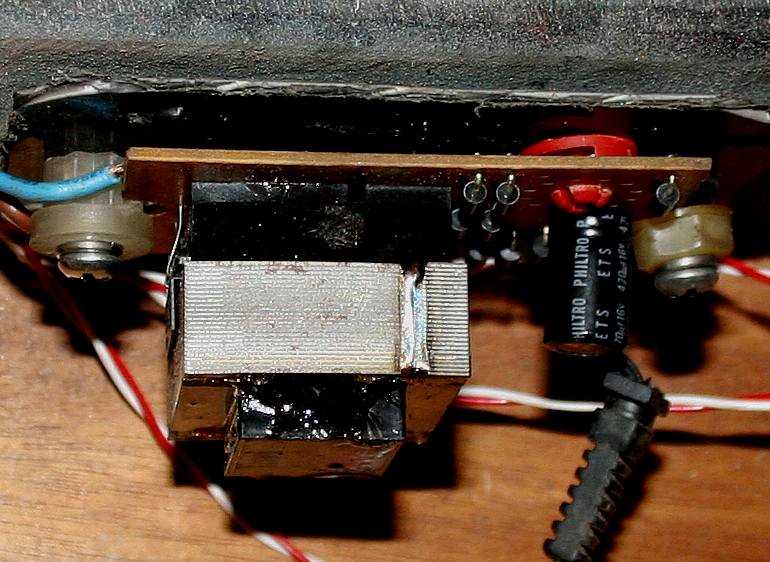
ELECTRICAL
- [LEFT] On-off and fused kettle lead socket are below the main chassis
of the stand on one side. The motor power pack is independently fused.
[RIGHT] We decided to use a separate step down transformer for the LED
lighting. You can switch this (Tandy) unit for different voltages,
between 3 and 9 volts. 4.5 volts worked best, but the unit ran a little
too warm for our liking - and you know how much we love large heat
sinks. Tandy, or Radio Shack, as it is known in the US has not been
around in the UK for many years after all 270 stores were sold to the
Carphone Warehouse in 1999. Tandy
still trade online. That is how old this recycled part is - but it still
works well - and with suitable heat dissipation finning it should give
years of trouble free service. Maplins
sell comparable products in stores all over the UK.
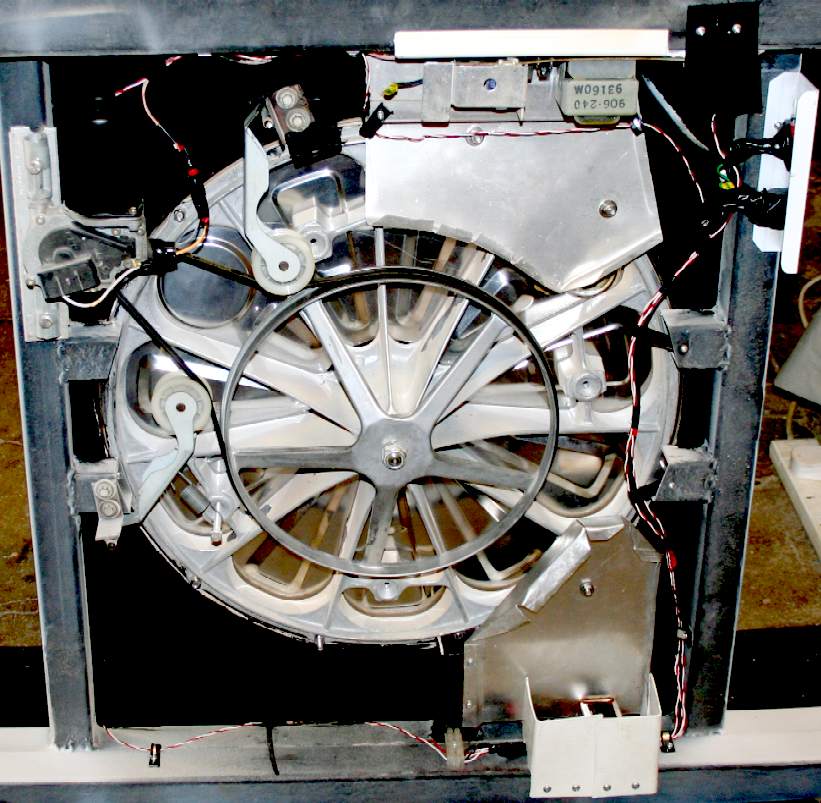
WIRING
- [LEFT] 5-11-15 Threading the low voltage cables to the LED lights. We
use choc blocks on the low voltage circuit to split the feed for four
spots. The lighting transformer ran a little hot for our liking, seen
here open to the elements for good airflow. [RIGHT] 6-11-15 We added a
large aluminium heat sink for the lighting transformer and added a
guard. Even after 4 hours of continuous operation the transformer was
only bearably warm - a great improvement. The harness was tidied up
under supervision of our Portable Electrical Appliance (PAT) tester, who
certified that this installation was safe.
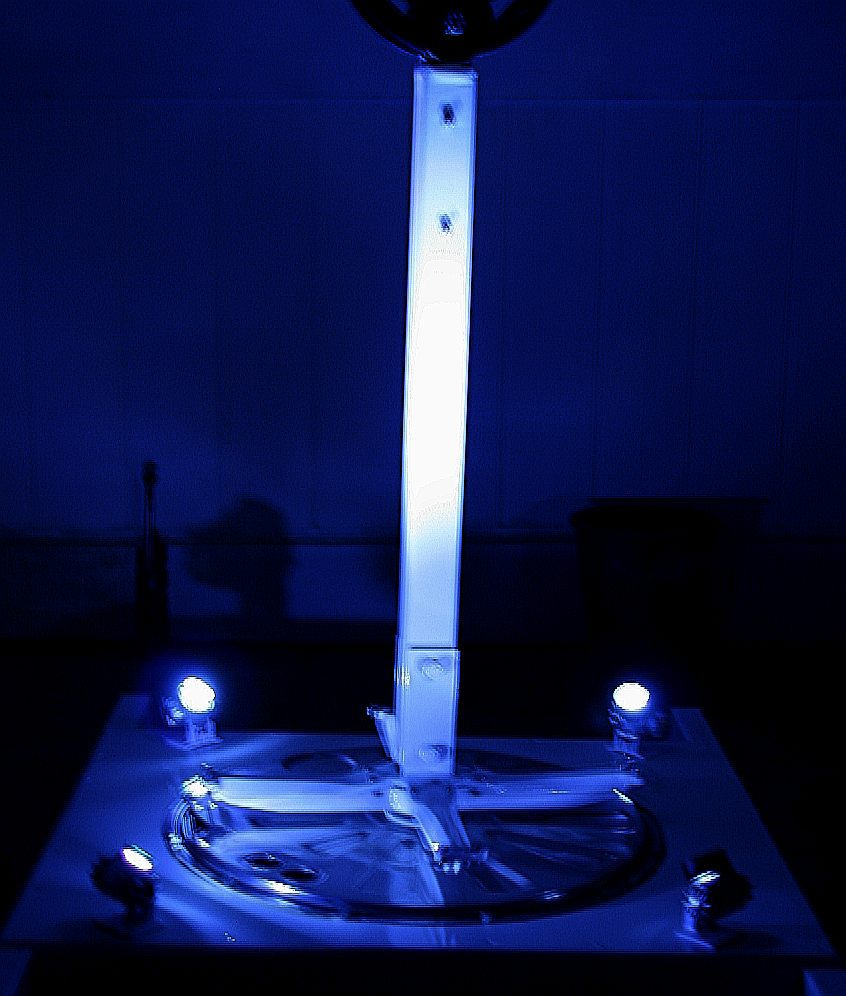
LIGHTING
DISPLAY - Testing out the spot lamps in low light conditions.
At night it can look a little Cathedral. Is that good or bad? Probably
good.
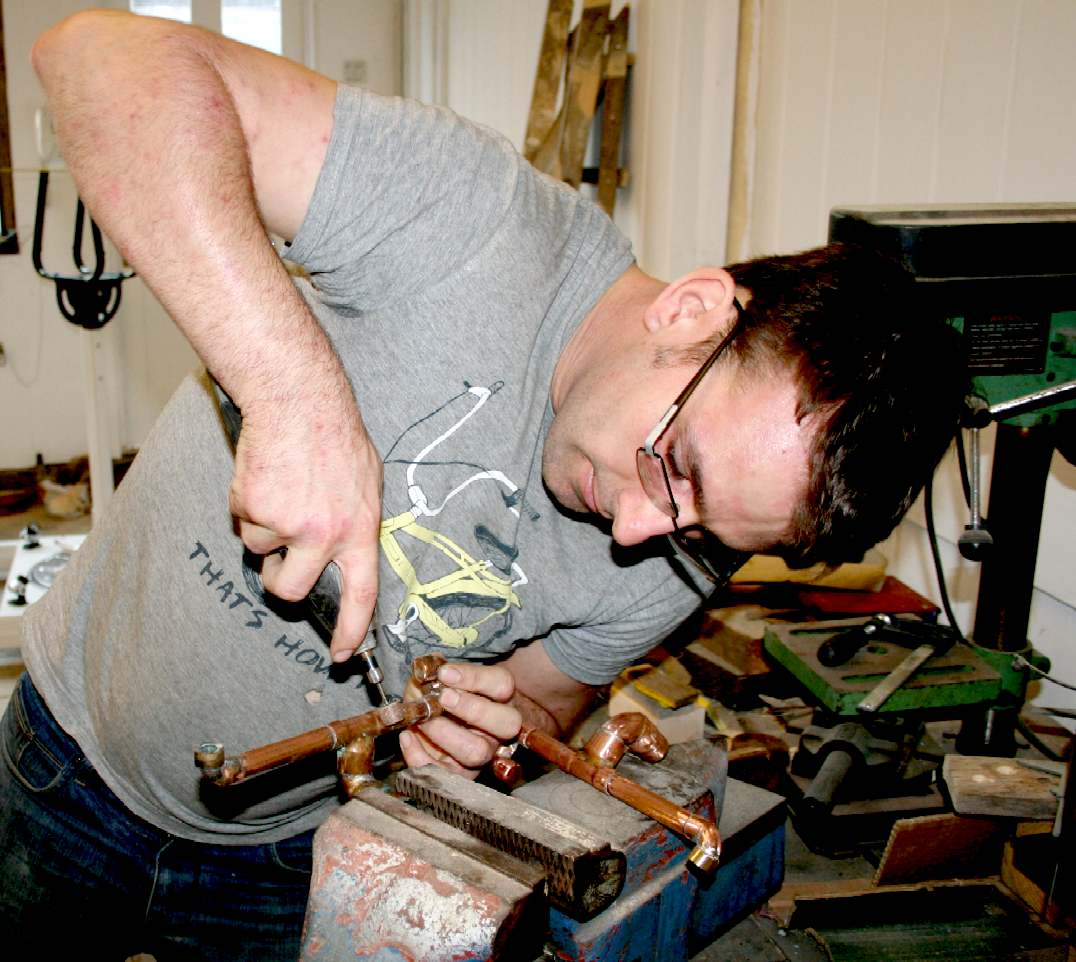
WORKSHOP
- Chris using a small grinding wheel to clean up some components for the
SeaVax project.
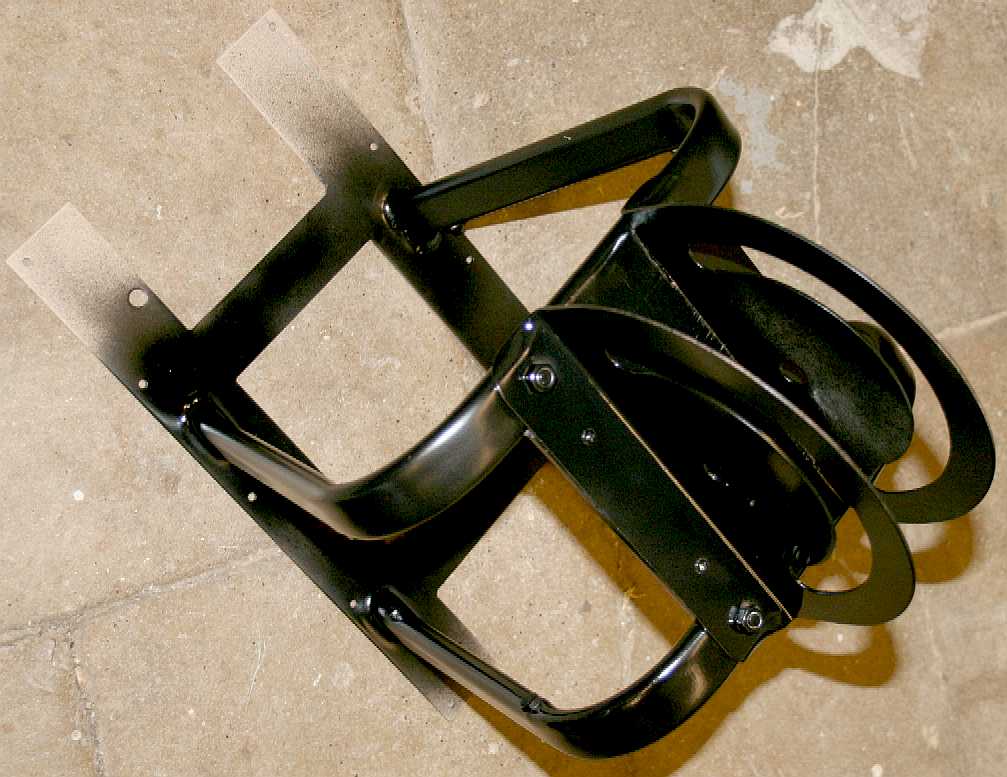
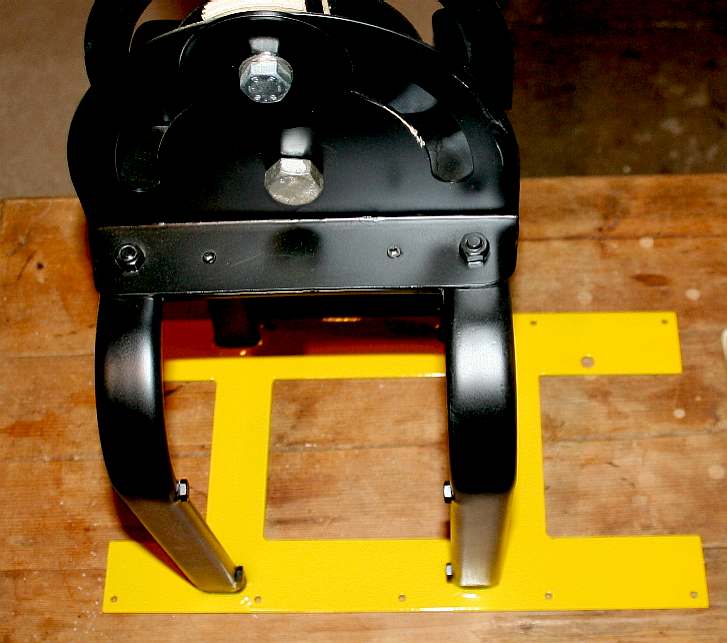
CRADLE
& SWIVEL - The cradle assembly must not detract from the ocean
cleaning head that passes through the middle of the cradle hoops. For this reason
the cradle is
painted matt black. Whereas the "H" base plate that attaches
to the underside of the deck should be the same machine yellow as the rest
of the boat on display. By this means the focus of visitors will be on the ocean
cleaning apparatus rather than the protection surrounding it. You can
see the painting sequence above. First paint the frame black, then mask
the cradle frame and paint the "H" plate machine yellow.
Simples. Be careful when removing the masking, not to get flakes of
paper or paint on the fresh surface.
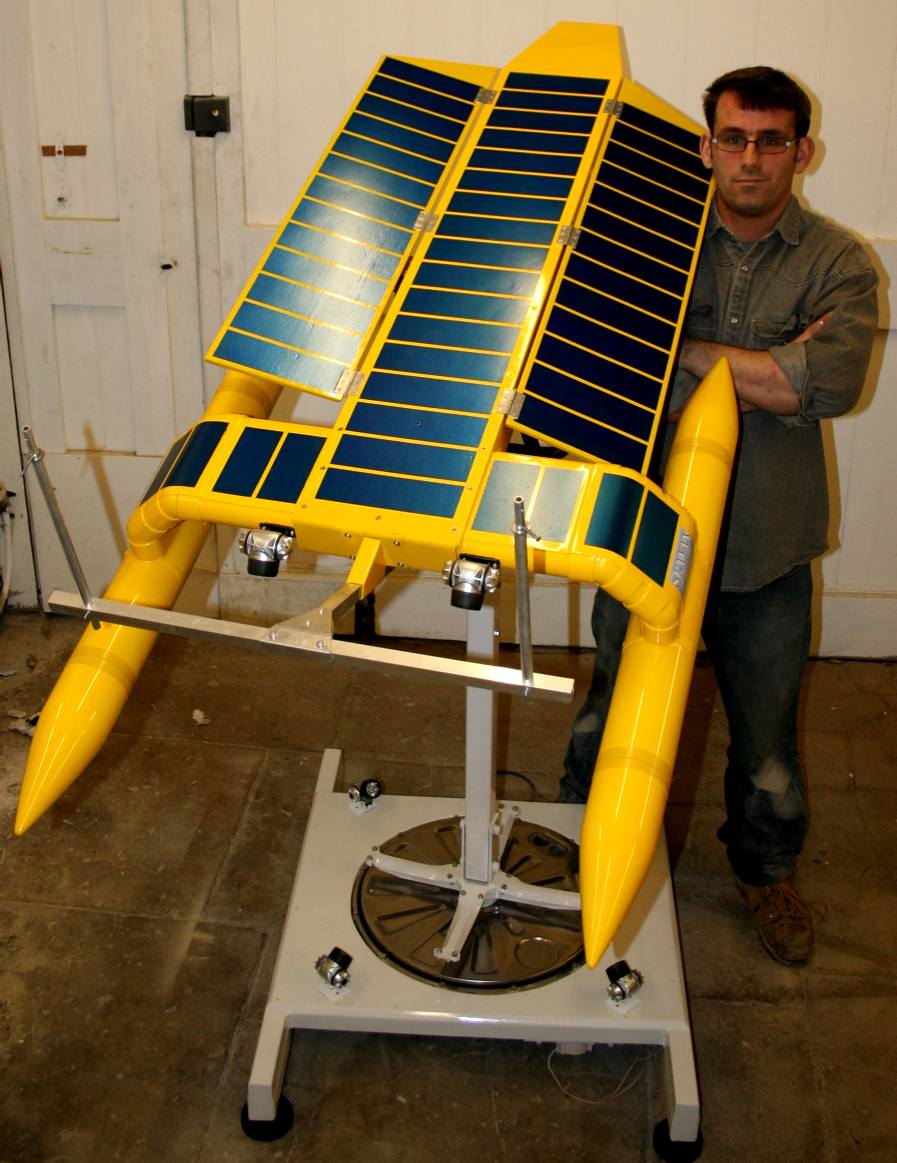
NOVEMBER
1 2015 - We are nearing completion on the stand. The hotel has been
booked and we are working out how best to transport the stand and
concept model to the show economically. We will be using a modified
super mini to get us to London and back with the smallest carbon
footprint practical.
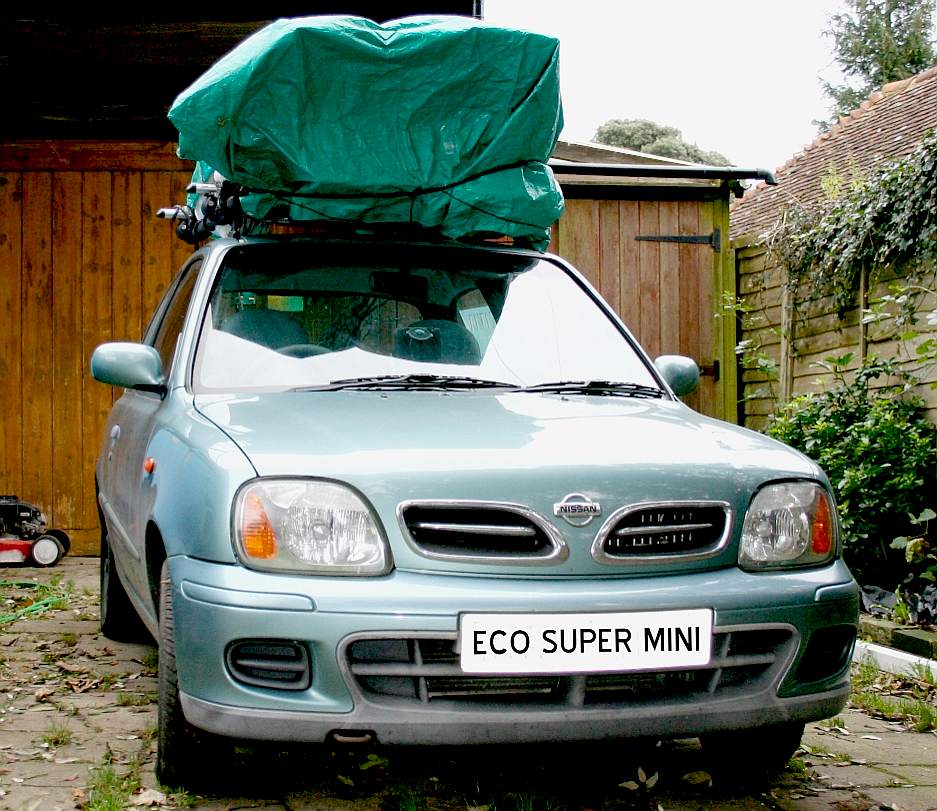
LOGISTICS -
The trip to London and back to Herstmonceux, which included a leg to
Woodford from Old Billingsgate twice, cost just £25 in fuel despite the
extra drag from the increased frontal area of the vehicle. Now that is
what we call economy motoring. Well done Nissan.
On top of this was the London Congestion Charge £11.50 and the Dartford
Crossing toll
charge £2.50. These add-ons were almost as much as the fuel. The
message is clear, stay away from old London town.
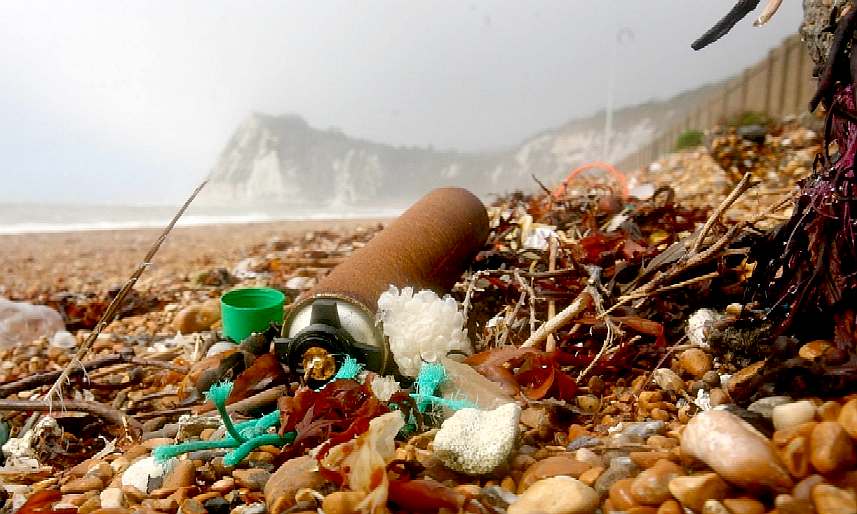
PLASTIC
BEACHES
- This is why we are going to all this bother: Rope, rusting cans,
styrofoam and bottle caps. They say "out of
sight, out of mind." And that is so true. That is why the ocean
gyres managed to build up to twice the size of Texas before anyone
started paying attention. We all need constant reminding of the harm we
are causing, especially politicians and businesses, who in the past
hoped that nobody would notice if they dumped all their rubbish out at
sea. The Marine Pollution Act
was supposed to change all that. Not so
far. Not one bit of it. Our politicians approved the legislation, but
secretly hoped that the ocean would self-clean.
THE
GUARDIAN 19 MARCH 2015
The number of wet wipes washing up on beaches in the UK
increased by more than 50% last year, say conservationists, who have
urged people to stop flushing them down their toilets.
The results of Marine Conservation Society’s (MCS)
annual beach cleanup, released on Thursday, found the number of wet
wipes more than doubled between 2013 and 2014. Thirty-five of the
non-biodegradable cleaning cloths were found for every kilometre of
beach.
The accumulation of wet wipes could be partly due to the severe
rainfall during the 2013-14 winter. Choked sewers may have flooded more
rubbish (including wet wipes) than usual into rivers, which ended up on
beaches. But Charlotte Coombes, an MCS conservation officer, said there
was a long-term increase in the number of cloths ending up in the
environment and on beaches in particular.
Coombes said: “This move towards convenience, the move towards
items to use once and throw away, it’s much easier for people to do
that. What we are doing is not just using a lot more resources we are
creating a lot more litter that can end up in the environment.”
Wet wipes are notorious for their impact on sewer systems, but
the impact on ecosystems is also a concern. Coombes said five of the
world’s seven remaining species of turtle regularly visit Britain’s
waters to feed in the cooler, nutrient-rich seas. Turtles often mistake
plastic bags for their natural jellyfish prey. But Coombes said wet wipes, which usually contain
plastic fibres, posed a similar danger.
“When marine wildlife eats that plastic, which they quite often
do, it just stays in the stomach of the animals and quite often they
just die of starvation,” she said.
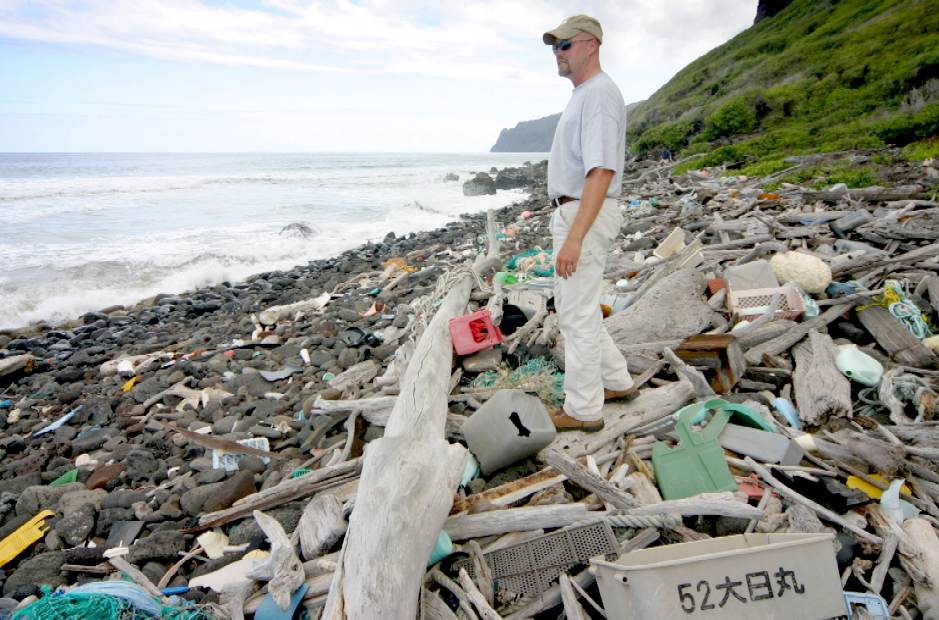
SHOCKING
- There are almost no beaches in the world where plastic waste in not a
problem. Humans are very messy animals who appears to care very little
for marine life. Plastic is even in the Arctic sea, with polar bears
coming into contact.
The predominant way for wipes to enter the environment is down
peoples’ toilets. Some brands of wet wipe are marked ‘flushable’, but
Coombes said:
“Our sewerage systems weren’t built to cope with wet wipes.
When flushed, they don’t disintegrate like toilet paper, and they
typically contain plastic so once they reach the sea, they last for a
very long time.”
Putting wet wipes down the toilet can cause blockages that lead
to disgusting buildups of fat, known as “fatbergs”. In 2013 a lump of
congealed fat the size of a bus was found in sewers beneath London. Earlier this year a spokesperson for Southern Water said Kent residents were dumping 2,000 tonnes of wet wipes into sewers. New York City has spent $18m (£12.3m) on “wipe-related equipment problems” in the past five years.
Blockages can also affect waterways by causing raw sewage to overflow into rivers and the ocean.
A spokeswoman for Keep Britain Tidy
said the most sustainable option was to stop using wet wipes
altogether, but failing that they should be disposed of appropriately.
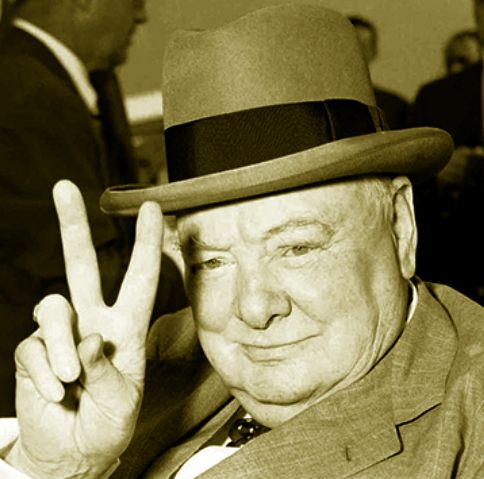
CALL
TO ARMS
- Yes, history repeats itself. Your country needs you to re-evaluate your
throwaway habits, the 1st World War poster featuring Lord Kitchener with
his dramatic moustache is spot on. "V" is for Vax, 'SeaVax,' in the fight against
ocean pollution. Sir Winston Churchill was right, we will fight the problem
on the beaches.
“We didn’t have wet wipes 30 to 40 years ago. People just used
flannels,” she said. “There’s three things that should go into a toilet.
Putting it crudely, they are pee, poo and paper. Nothing else. Put it
in the bin.”
During a weekend last September, more than 5,000 MCS volunteers
gathered and catalogued 2,457 pieces of litter for every kilometre of
coastline they scoured. This was an increase of 6.4% from 2013.
MCS said the government should act to halt the increase in beach
rubbish. The society called for a policy that targeted the main sources
of marine litter – the public,
fishing, shipping and sewage-related debris (including wet wipes).
The increase in litter was not uniform. The south-west saw an increase
of 89% in litter, in Wales the increase was 46%. In
Scotland and northern England less rubbish was found than in 2013.
A spokeswoman for Energizer Group, which manufactures Wet Ones,
said the company includes a logo on the packaging advising customers not
to flush them down the toilet.
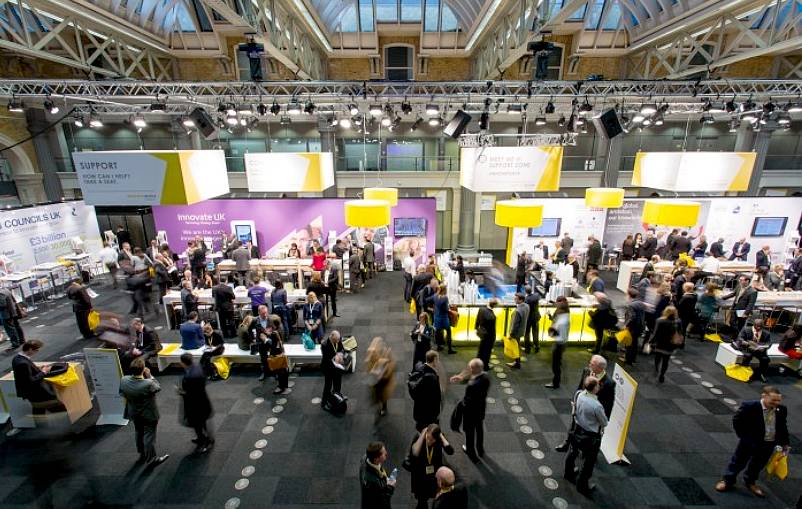
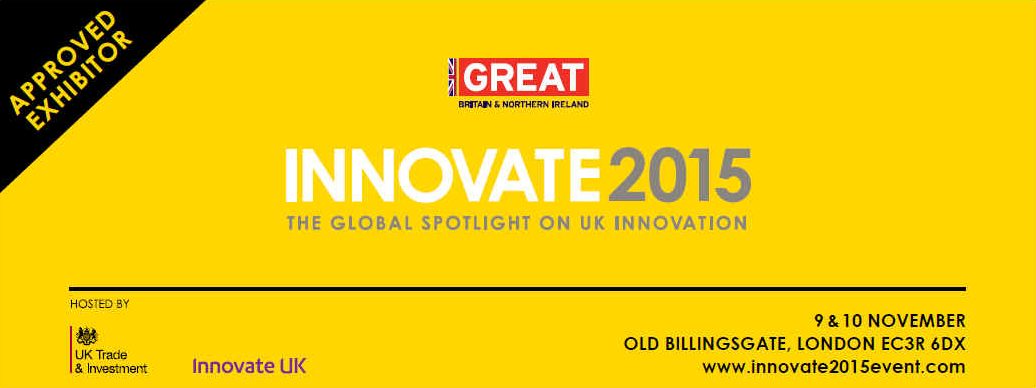
OLD
BILLINGSGATE
- Bluebird Marine Systems were an approved exhibitor for Innovate2015.
Never mind the declining fish stocks and toxins in our food chain in
2015, it is far worse in 2024. Having proved the concept,
the team lobbied hard and made three application for EU
funding, two applications for UK funding. The sad truth is
that nobody wanted to pay to clean up the ocean - which is
after all a free dumping ground at the moment. So, why pay
to develop a solution? Beach cleaning by armies of
volunteers is wonderful work, but does not scratch the
surface of the problem. Plastic production is on the
increase. So to is chemical dumping in the ocean. With micro
plastic particles acting like sponges. It is a great pity
that SeaVax was not funded, as being the only system to
provide a way of harvesting toxic plastics in large volumes.
A virtual chemical trapping and filtration system, all in
one. Also useful for sargassum
sequestration and geodata harvesting. The dream team were
forced to disband without any commitment, to resume their
normal lives and catch up with their mortgage payments.
This tells us that European
standards are not taking into account plastic
pollution. Hence, not requiring local authorities to do anything
about the rubbish on their doorstep. The problem with local authorities
is that unless you tell them to do something - usually with the threat
of some serious penalties, they will not be proactive.
SEAVAX
OCEAN CLEANING DRONE
- Like a scene from the
'Thunderbirds'
television series and
International Rescue, a vessel like the SeaVax autonomous ocean
dustcart, could offer a
solution to ocean pollution. The proof of concept model demonstrated
that the design worked in controlled test tank conditions. The world was not ready to pay to clean up their
free dumping ground. Just how polluted and toxic would fish have to be,
before wallets are opened.